Un service de maintenance répare quand une panne survient. Oui, mais une gestion des problèmes au cas par cas génère des surcoûts, des retards de production et, par conséquent, une baisse de productivité, sans compter la fatigue des techniciens. La maintenance industrielle a donc un rôle prépondérant à jouer dans la stabilité économique de l’industrie du futur.
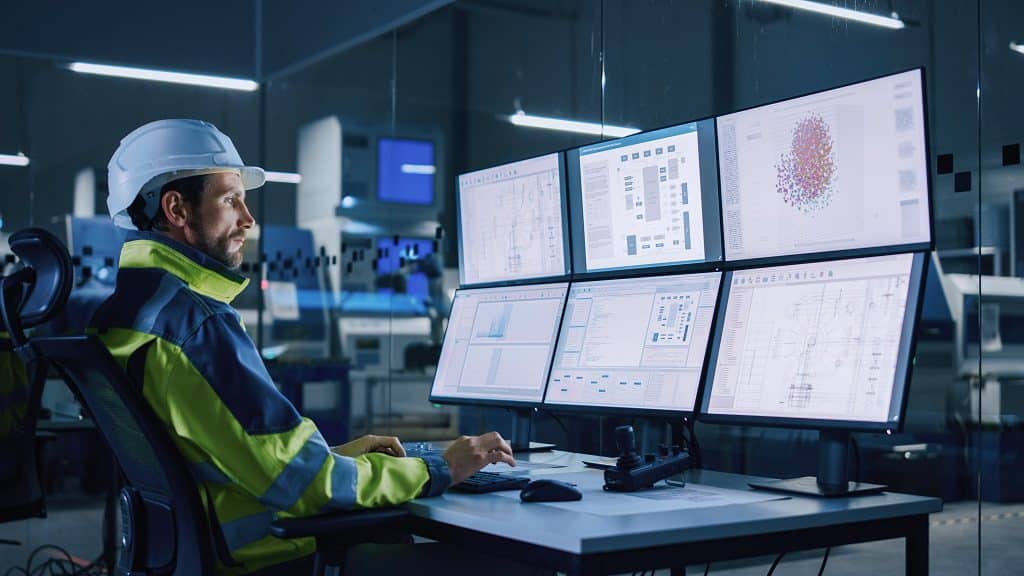
L’industrie est un secteur toujours en évolution. Et, pour assurer une stabilité et une performance synonymes de pérennité, l’industrie doit absolument veiller à ce que ses rouages soient bien huilés. Il est donc fondamental pour elle de chercher à améliorer sa qualité de service dans l’immédiat et pour le futur. De ce fait, la maintenance tient une place clé dans ce processus de recherche de performance. Mais, comment gérer intelligemment et efficacement un service de maintenance ? Guy Besson, expert en organisation et fiabilisation en maintenance industrielle, nous explique comment passer d’une maintenance corrective à une maintenance préventive.
La maintenance préventive : quels enjeux ?
Dans un souci d’économie et de rentabilité, les entreprises cherchent à réduire les budgets. Pour autant, les coupes budgétaires (quand elles sont bien pensées) ne sont pas nécessairement pénalisantes. Et c’est bien cet équilibre qui caractérise les enjeux des services de maintenance, qui voient plutôt leurs budgets exploser quand la gestion des pannes se fait au cas par cas, sans réelle politique de fond. Ainsi, une coupe budgétaire accompagnée d’une démarche d’amélioration pertinente peut porter ses fruits.
Lancer une démarche d’optimisation de coût répond à l’objectif QCD : qualité irréprochable, coûts optimisés, délais respectés… en prévoyant les incidents techniques plutôt qu’en les subissant. On estime que les coûts de maintenance peuvent représenter jusqu’à 50 % des coûts de production. Une démarche préventive permettrait alors une réduction des coûts et du nombre de pannes, un investissement moindre dans de nouvelles machines et une mobilisation plus efficace des techniciens.
Structurer sa démarche de maintenance préventive
Informatique, mécanique… Tous les appareils, outils et machines nécessitent de la maintenance. Il s’agit bien là d’un domaine qui allie des connaissances théoriques des différents types de machines, des compétences ainsi que des savoir-faire techniques et pragmatiques très souvent acquis par l’expérience. Mais cette connaissance par l’expérience comporte généralement un défaut : elle est souvent plus difficile à structurer pour être méthodique et transmissible. Alors que toute démarche de maintenance demande de la méthode.
Les huit indispensables de la maintenance
Ces indispensables assurent une organisation presque sans faille et constituent le premier pas vers un service organisé :
- une matrice des équipements réalisée et utilisée ;
- l’efficience des ressources (techniciens, outillage, fournisseurs) ;
- des pièces de rechange rangées et codifiées pour les trouver en moins de 1 minute ;
- des analyses de panne effectuées (utiliser les bons outils pour comprendre l’origine des pannes) ;
- la mise en place de bons indicateurs de suivi ;
- le graissage et la vidange des machines sous contrôle ;
- la rédaction de procédures pour toutes les actions et tous les processus de maintenance que le service réalise (actions, nomenclatures, organisation…) ;
- une documentation organisée et trouvable immédiatement.
Deux piliers pour structurer ces indispensables
La dynamique générée par ces huit indispensables s’accompagne, selon notre expert, de deux piliers qui ne peuvent pas être négligés pour l’optimisation des ressources.
Le premier pilier n’est autre que la matrice présente dans les huit indispensables. En effet, classer les machines (selon différents critères propres à l’activité) permet d’obtenir une liste par ordre de criticité. Et donc de connaître les machines les plus « à risque » ou celles qui sont prioritaires dans un travail de maintenance de fond.
Le deuxième pilier est la règle des 80/20. C’est-à-dire que 80% des risques sont concentrés sur 20% des machines les plus à risque. Cette règle permet une politique de maintenance et de restauration plus soutenue, de limiter le risque de panne en plus d’optimiser l’utilisation de toutes ces ressources (outillage, personnel, etc.).
Il s’agit donc d’être au fait de ces éléments de façon à réduire la charge de travail en évitant de se laisser submerger par les pannes évitables.
Maîtriser les cinq causes de panne
Que ce soit pour des raisons d’organisation, de compte à rendre ou de compétences, la réparation n’est plus suffisante dans un environnement qui demande d’être compétitif. Or, les pannes à répétition sur une même machine entament considérablement le potentiel de rentabilité. Aussi, comprendre l’origine d’une panne est fondamental. Dans le domaine de la maintenance, c’est même la base d’un travail de fond bien fait. En effet, connaître la cause d’une panne permet d’y apporter une solution et donc de maîtriser une partie des risques.
- une mauvaise utilisation des équipements : trop vite, trop fort, avec le mauvais matériau…
- un mauvais entretien de la machine : c’est la responsabilité de son utilisateur qui doit veiller à la nettoyer, remarquer une usure, etc.
- une insuffisance dans la maintenance : une pièce pas changée à temps, une vidange tardive, etc.
- le facteur humain : souvent assimilé à un problème de compétences, il peut s’agir d’une réparation mal faite, d’une étourderie, etc.
- un défaut de conception.
« À chaque problème, sa solution » et c’est bien ce que permet ce travail d’analyse. La bonne compréhension d’une panne est la clé pour une ressource de maintenance adéquate.
Bien appréhender la résolution de problème
La résolution de problème se construit en trois étapes clés :
- poser le problème ;
- chercher les causes clés ;
- lancer le plan d’action.
Une fois le diagnostic posé, il convient d’apporter une solution efficace et appropriée. C’est-à-dire qui correspond à l’investissement nécessaire qu’on peut y consacrer (temps, budget, ressource…) dans la limite de ce qui est rentable et permet au service de maintenance d’être efficace. Trois outils peuvent répondre à ce besoin :
- le JDI : « just do it » est pertinent pour les petits problèmes qu’on peut résoudre dans l’heure, sans validation hiérarchique, sans commande d’outillage, etc. Un problème résolu en 1 heure par un technicien.
- la méthode MARP ou quick Kaizen : la roue de l’amélioration, issue du lean management, combine différents outils d’analyse et de planification de résolution de problème (QQOQCCP, les 5 pourquoi, le diagramme d’Ishikawa). Elle peut être le début d’un plan d’action et correspond donc davantage à des soucis de maintenance profonds ou répétitifs. Cette méthode s’applique aux problèmes de complexité moyenne : 1 à 2 jours pour un à deux techniciens.
- le 8D (D pour discipline, c’est-à-dire « action à réaliser »): il s’agit d’une méthode d’analyse en 8 étapes qui structure la prise de décision dans un processus d’amélioration continue. Ses différentes étapes permettent de prendre en compte toutes les facettes du problème à résoudre et font appel à l’esprit collaboratif avant tout. Plus structurée, elle concerne davantage les problèmes plus complexes qui concernent différentes ressources (service qualité, bureau d’études…), avec trois à cinq personnes et à planifier une durée plus longue (environ 1 à 4 mois).
L’organisation du traitement des pannes ouvre la voie vers le « zéro panne » en structurant la démarche et en exigeant une analyse complète d’un problème afin d’y répondre durablement.
Focus sur la formation
Les services de maintenance, faute de temps et de recul, travaillent généralement à flux tendu dans une pratique de maintenance corrective. Or, pour faire de réelles économies et un retour sur investissement intéressant, les entreprises doivent passer à une logique de maintenance préventive.
La formation Déployer le pilier TPM : la maintenance planifiée aborde les différents outils permettant cette maintenance préventive, en s’appuyant toujours sur les expériences professionnelles des participants. En dressant des diagnostics personnalisés et en faisant appel à l’intelligence collective, nous cherchons à porter les participants vers une analyse méthodique de leurs pannes et vers l’élaboration d’un plan d’actions pertinent pour leur activité et leurs machines en répondant à leurs besoins. Et c’est bien là tout l’enjeu de notre programme : savoir adapter ces différents outils à la résolution de panne tout en apprenant à projeter LE plan d’actions qui fera faire des économies à l’entreprise.
La maintenance préventive réunit tous les atouts pour aider l’industrie à gagner en performance et en rentabilité. Grâce à des méthodes et à des outils pertinents, les investissements auront rapidement un effet sur la force de travail des équipes (et leur motivation), autant que sur la durée de vie des machines. Enfin, cette logique de politique de maintenance ne demande qu’à s’inscrire dans l’évolution de l’industrie avec, notamment, les progrès technologiques qui permettent dans certains cas de mettre en œuvre une politique de maintenance prédictive.