Lean management and Six Sigma® are improvement methodologies you've probably already heard of. In fact, they have become essential in companies in general and in industry in particular. Between the search for optimisation and the need for efficiency, companies have every interest in developing new approaches aimed at performance at all levels of production. While recalling the main principles of Lean and Six Sigma®, Industry expert Frédéric Rouzeau shows us how they complement each other and are closely linked to Industry 4.0.
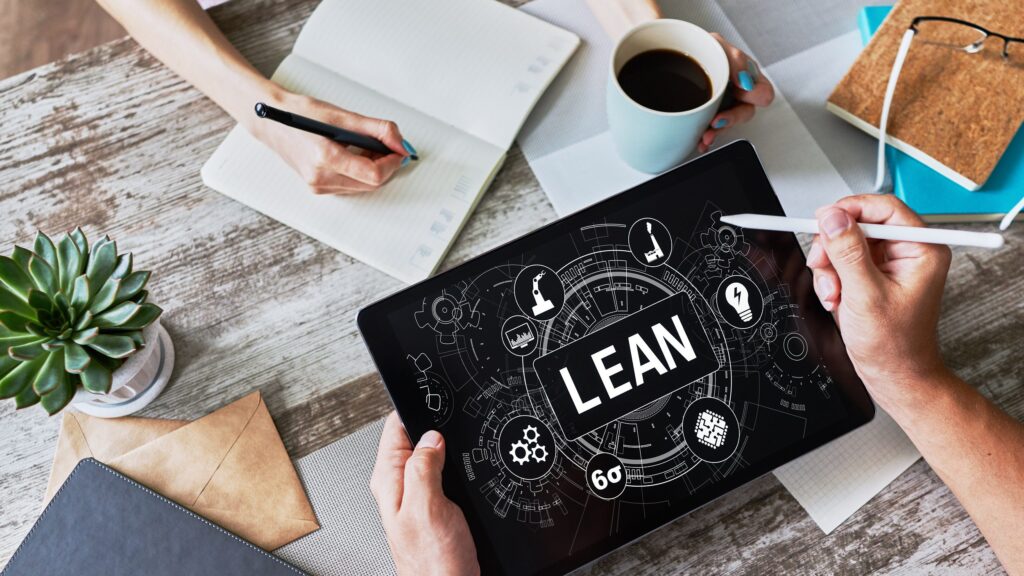
The Lean method: origins and principles
In the 1950s, Taiichi Ohno, Toyota's industrial director, implemented the Toyota Production System (TPS), a new way of managing industrial activities. Its main objective was to eliminate any activity that does not add value for customers.
In the early 1980s, a team of MIT researchers led by James P. Womack studied Toyota's success. They quickly became convinced that Toyota's TPS could be applied in all companies, in all sectors and in all countries. They decided to call this new approach "lean", a term that perfectly illustrates this obsessive pursuit of the various forms of waste within processes.
In 1991, James Womack and two other MIT researchers published The Machine That Changed the World (Harper Collins, 1991), which presents their conclusions from the study of Toyota's TPS. This book contributes to the deployment of lean manufacturing It is still the benchmark for industrial management. Lean management has since spread widely across all sectors of activity (industry, services, offices, health, etc.).
Lean management: a global vision of industry
This type of management relies on the strong involvement of all staff. They are mobilised in teams to identify and propose improvements aimed at eliminating waste. Waste can take three different forms depending on its nature:
- Muri: the saturation of a resource, a task that is excessive, too difficult or even impossible;
- Mura: irregularities, variability ;
- Muda: tasks with no added value. These can be divided into eight different types:
- overproduction (producing too much or too soon): the worst of all because it generates all the others;
- unnecessary stocks;
- unnecessary transport and handling (of products);
- over-processing (superfluous operations, over-quality) ;
- unnecessary movement and travel (by employees) ;
- errors, defects and rejects ;
- waiting time and delays ;
- under-utilisation of skills.
The Six Sigma® method: origins and principles
The Six Sigma ® method is slightly more recent. It originated in the late 1980s when Bill Smith, an engineer at Motorola, developed it to improve manufacturing processes and the quality of their products. The aim was to improve customer satisfaction. The method became famous in the 90s, thanks to General Electric and its charismatic chairman Jack Welch. It was he who decided to improve it and apply it throughout the GE group with resounding success.
The Six Sigma® method aims to reduce process variability to eliminate or reduce the risk of the product (or service) being rejected by its recipient on the pretext that it does not meet expectations or specifications. This method relies mainly on statistical tools to identify and control the parameters product or process. It is deployed in project mode, managed by a Green or Black Belt certified project manager. It is structured into five distinct phases: Define, Measure, Analyse, Improve, Control, or DMAIC.
Each stage of the DMAIC project has specific objectives and uses different tools:
- Define These include framing the project, identifying operational and financial gains, understanding customer expectations and CTQs (critical to quality), also known as Yi, mapping the process, etc;
- Measure List the potentially influential factors in the process (called Xi) and simultaneously measure Yi and Xi after ensuring the reliability of the measurement processes;
- Analyze Perform a data analysis to identify the Xi factors that have the greatest influence on the Yi (responses);
- Improve Find ways of improving the most influential Xi;
- Check Process management tools such as statistical process control (SPC).
Lean-Six Sigma®
With their main point in common (customer focus), the two methodologies were combined in the early 2000s to give rise to Lean-Six Sigma® (LSS). The two approaches complement each other enormously:
Lean
- practical and pragmatic
- flow orientation
- eliminate waste
- Improve through organisation (involvement)
- continuous improvement (day-to-day)
- process improvement
Six Sigma®
- analytical and statistical
- quality orientation
- improve value-added activities
- improving organisation
- disruptive improvement (project mode)
- process improvement
But how can this combination of methods be applied in practice in the field of Industry 4.0? What are the specific features of this field that make them particularly relevant?
Industry 4.0
L'industry 4.0Digitalisation, also frequently referred to as the "connected factory", marks the fourth industrial revolution, following on from mechanisation (1.0), mass production (2.0) and automation (3.0). Thanks to digitalisation, industry is becoming an interconnected global system. Organised into technological building blocks, the many innovations have a direct or indirect impact on all industry functions. Here are a few examples of the most frequently encountered building blocks:
- Efficient processes (advanced machining, additive manufacturing, etc.);
- automation, handling systems ;
- measurement and analysis of product data (real-time connected sensors, etc.);
- Communicating workstations and machines (connected operator, augmented reality, MES (Manufacturing Execution System), intelligent and collaborative machines, etc.);
- digital mock-up (product/process simulation, digital mock-up, digital twin, virtual reality, etc.);
- the predictive maintenanceconnected machine maintenance ;
- steering and management of the company (collaborative working, workflow/EDM (electronic document management), etc.).
What are the links between Lean, Six Sigma® and Industry 4.0?
It is unthinkable to deploy a technological brick without first having a strong culture of lean within the company. This is becauseeven when automated, waste is still waste. This applies in particular to handling and storage.
Conversely, certain building blocks will make a major contribution to strengthening the Lean method. Here are a few examples:
- Augmented reality: it can prevent or detect errors;
- real-time performance management ;
- communicating machines and connected operators: they simplify monitoring and traceability;
- Robotics and automated materials handling: they reduce drudgery;
- operator training using virtual or augmented reality;
- accessibility and reliability of working documents thanks to EDM.
As far as Six Sigma® is concerned, the link with MES, intelligent and collaborative machines, predictive maintenance, efficient processes, etc. is obvious, as identifying and monitoring key parameters seems essential. It is therefore highly likely that 4.0-type solutions will be considered during the DMAIC improvement phase.
By adopting 'modern' technological tools and processes, Industry 4.0 is a perfect breeding ground for the application of Lean Six Sigma® and its quest to eradicate the superfluous. What's more, by analysing each stage of production using the DMAIC methodology, Industry 4.0 is fully committed to optimisation.
So on the one hand, we have an approach aimed at the systematic improvement of processes (Lean) and, on the other, a method whose objective is to reduce all forms of variation (Six Sigma®). Combining these two concepts, Lean Six Sigma® enables the continuous improvement of processes while placing the customer at the centre of concerns, and is a clear path towards excellence. However, Lean Six Sigma® is part of a quality approach that can only work and endure with management support and strong employee awareness. In other words, Industry 4.0 cannot do without a more collaborative organisation and training for the key players in the project.