Le Lean management et le Six Sigma® sont des méthodologies d’amélioration dont vous avez certainement déjà entendu parler. Elles sont, en effet, devenues incontournables dans les entreprises en général et dans l’industrie en particulier. Entre recherche d’optimisation et besoin d’efficacité, les entreprises ont tout intérêt à développer de nouvelles approches visant la performance à tous les niveaux de production. Tout en rappelant les grands principes du Lean et du Six Sigma®, Frédéric Rouzeau, expert dans le domaine de l’industrie, nous démontre leur grande complémentarité et leur lien étroit avec l’industrie 4.0.
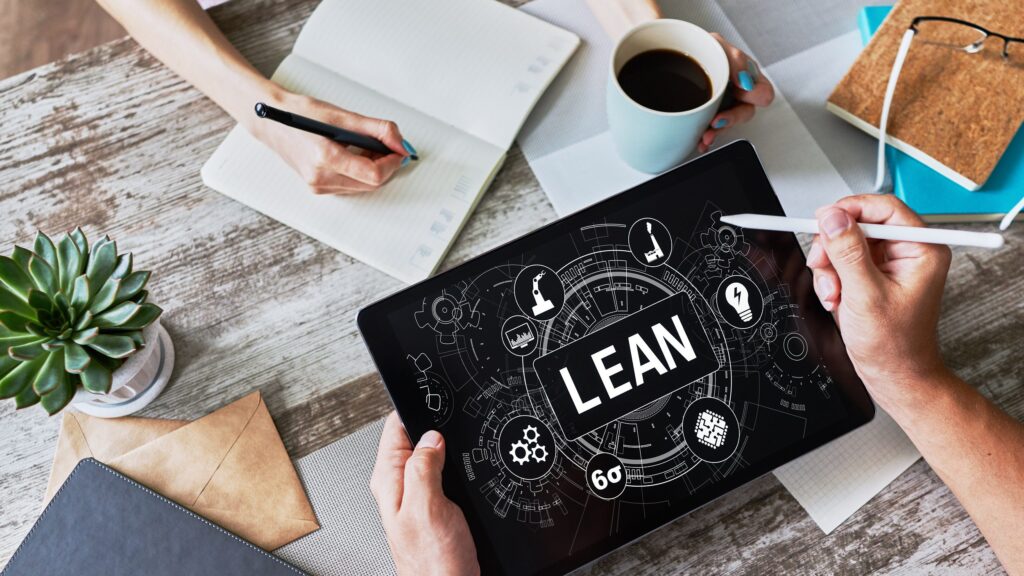
La méthode Lean : origines et principes
Dans les années 1950, Taiichi Ohno, directeur industriel de Toyota, met en œuvre le Toyota Production System (TPS), un nouveau mode de gestion des activités industrielles. Son objectif principal consiste alors à éliminer toute activité n’ajoutant pas de valeur aux yeux des clients.
Au début des années 1980, une équipe de chercheurs du MIT pilotée par James P. Womack, se penche sur la réussite de Toyota. Ils ont très rapidement la conviction que le TPS de Toyota est applicable dans toutes les entreprises de tous les secteurs et de tous les pays. Ils décident de baptiser cette nouvelle approche « lean » (« maigre », « sans gras », en français), terme qui illustre parfaitement cette traque obsessionnelle des différentes formes de gaspillage au sein des processus.
En 1991, James Womack et deux autres chercheurs du MIT publient The Machine That Changed the World (Harper Collins, 1991), qui présente leurs conclusions de l’étude du TPS de Toyota. Cet ouvrage contribue au déploiement du lean manufacturing à travers le monde et reste, encore aujourd’hui, un ouvrage de référence en matière de gestion industrielle. Le Lean management s’est, depuis, largement répandu dans tous les secteurs d’activités (industrie, services, office, santé, etc.).
Le Lean management : une vision globale de l’industrie
Ce type de management s’appuie sur la forte implication de l’ensemble du personnel. Celui-ci va se mobiliser en équipes pour identifier et proposer des améliorations visant à éliminer les gaspillages. Ces derniers peuvent prendre trois formes différentes selon leurs natures :
- Muri : la saturation d’une ressource, une tâche excessive, trop difficile voire impossible ;
- Mura : les irrégularités, la variabilité ;
- Muda : les tâches sans valeur ajoutée. Celles-ci peuvent elles-mêmes être réparties en huit types différents :
- la surproduction (produire trop ou trop tôt) : le pire de tous car à lui seul il génère tous les autres ;
- les stocks inutiles ;
- les transports et les manutentions inutiles (des produits) ;
- le surprocessing (les opérations superflues, la surqualité) ;
- les mouvements et les déplacements inutiles (des collaborateurs) ;
- les erreurs, défauts et rebuts ;
- le temps d’attente et les délais ;
- la sous-utilisation des compétences.
La méthode Six Sigma® : origines et principes
La méthode Six Sigma ® est un peu plus récente. Elle trouve son origine à la fin des années 1980 lorsque Bill Smith, ingénieur chez Motorola, l’a développée pour améliorer les processus de fabrication et la qualité de leurs produits. Il s’agissait alors de mieux satisfaire les clients. La méthode devient célèbre dans les années 90, grâce à General Electric et son charismatique président Jack Welch. En effet, c’est lui qui a décidé de l’améliorer et de l’appliquer dans tout le groupe GE avec un succès retentissant.
La méthode Six Sigma® a pour but de réduire la variabilité des processus pour éliminer ou réduire le risque de voir le produit (ou service) rejeté par son destinataire sous prétexte qu’il est en dehors des attentes ou spécifications. Cette méthode s’appuie principalement sur des outils statistiques qui vont permettre d’identifier et de mettre sous contrôle les paramètres clés du produit ou du processus. Elle se déploie en mode projet : pilotage par un chef de projet certifié Green ou Black Belt. Elle se structure en cinq phases distinctes : Define, Measure, Analyse, Improve, Control, c’est le « DMAIC ».
Chaque étape du projet DMAIC a des objectifs spécifiques et fait appel à des outils différents :
- Définir : cadrer le projet, identifier les gains opérationnels et financiers, comprendre les attentes des clients et les CTQ (critical to quality) appelés aussi Yi, cartographier le processus… ;
- Mesurer : lister les facteurs potentiellement influents du processus (appelés Xi) et mesurer simultanément les Yi et Xi après s’être assuré de la fiabilité des processus de mesure ;
- Analyser : réaliser une analyse de données pour identifier les facteurs Xi les plus influents sur les Yi (réponses) ;
- Améliorer : trouver des actions d’améliorations relatives aux Xi les plus influents ;
- Contrôler : mettre en place des outils de pilotage du processus tels que la MSP (maîtrise statistique des procédés).
Le Lean-Six Sigma®
Fortes de leur principal point commun (l’orientation « client »), les deux méthodologies ont été associées au début des années 2000 pour donner naissance au Lean-Six Sigma® (LSS). On trouve en effet énormément de complémentarité entre ces deux approches :
Lean
- pratique et pragmatique
- orientation flux
- supprimer les gaspillages
- améliorer grâce à l’organisation (implication)
- amélioration continue (au jour le jour)
- amélioration des processus
Six Sigma®
- analytique et statistique
- orientation qualité
- améliorer les activités à valeur ajoutée
- améliorer l’organisation
- amélioration en rupture (en mode projet)
- amélioration des procédés
Mais comment la mise en œuvre de cette combinaison de méthodes s’applique-t-elle concrètement dans le domaine de l’industrie 4.0 ? Quelles sont les spécificités de ce domaine qui les rendent particulièrement pertinentes ?
L’industrie 4.0
L’industrie 4.0, aussi fréquemment nommée « usine connectée », marque la quatrième révolution industrielle, après celle de la mécanisation (1.0), celle de la production de masse (2.0) et celle de l’automatisation (3.0). Grâce à la numérisation, l’industrie devient un système global interconnecté. Organisées en briques technologiques, les nombreuses innovations ont un impact directement ou indirectement sur l’ensemble des fonctions de l’industrie. Quelques exemples parmi les briques les plus fréquemment rencontrées :
- les procédés efficients (usinage avancé, fabrication additive…) ;
- l’automatisation, la transitique ;
- la mesure et l’analyse des données produits (capteurs connectés temps réels…) ;
- les postes de travail et les machines communicantes (opérateur connecté, réalité augmentée, MES (Manufacturing Execution System), machines intelligentes et collaboratives…) ;
- la maquette numérique (simulation produit/process, maquette numérique, jumeau numérique, réalité virtuelle…) ;
- la maintenance prédictive, la maintenance connectée des machines ;
- le pilotage et la gestion de l’entreprise (travail collaboratif, workflow/GED (Gestion électronique documentaire)…).
Quels liens entre le Lean, le Six Sigma® et l’industrie 4.0 ?
Il est inenvisageable de déployer une brique technologique sans disposer préalablement d’une forte culture lean au sein de l’entreprise. En effet, même automatisé, un gaspillage reste un gaspillage. Cela s’applique en particulier aux manutentions et aux stockages.
À l’inverse, certaines briques vont fortement contribuer au renforcement de la méthode Lean. Quelques exemples :
- la réalité augmentée : elle peut éviter ou détecter les erreurs ;
- le pilotage en temps réel de la performance ;
- les machines communicantes et opérateurs connectés : ils simplifient le suivi et la traçabilité ;
- la robotique, la transitique : elles réduisent la pénibilité ;
- la formation des opérateurs à l’aide de la réalité virtuelle ou augmentée ;
- l’accessibilité et la fiabilité des documents de travail grâce à la GED.
Concernant le Six Sigma®, le lien avec le MES, les machines intelligentes et collaboratives, la maintenance prédictive, les procédés efficients… est évident car identifier et suivre les paramètres clés apparaît comme essentiel. Il est donc fort probable que lors de la phase d’amélioration du DMAIC, des solutions de type 4.0 soient envisagées.
En s’appropriant des outils technologiques et des process « modernes », l’industrie 4.0 est un terrain tout trouvé pour l’application du Lean Six Sigma® et sa recherche d’éradication du superflu. De plus, en analysant chaque étape de production selon la méthodologie DMAIC, l’industrie 4.0 entre pleinement dans l’optimisation.
Nous avons donc d’un côté, une démarche visant l’amélioration systématique des processus (Lean) et, de l’autre, une méthode dont l’objectif est de réduire toutes les formes de variation (Six Sigma®). Combinaison de ces deux concepts, le Lean Six Sigma® permet l’amélioration continue des processus tout en plaçant le client au centre des préoccupations et se fait voie toute tracée vers l’excellence. Toutefois, le Lean Six Sigma® s’inscrit dans une démarche qualité qui ne peut fonctionner et perdurer qu’avec le soutien du management et une sensibilisation forte des collaborateurs. Autrement dit, l’industrie 4.0 ne peut pas faire l’impasse sur une organisation plus collaborative et la formation des acteurs clés du projet.