As a key position in the supply chain, the role of the procurement officer is evolving from managing emergencies to becoming a key player in the supply chain. role more strategic anticipation. In a volatile environment, marked by crises and stock-outs, the supply chain needs to develop its ability to anticipate and respond. resilience. And this means, in particular, increasing the digitalisation of the supply chain. It also means acquiring new skills, particularly in data management and analysis. So what are the new challenges facing the profession? How do you get into the supply chain? What are the attractions and constraints of the job?
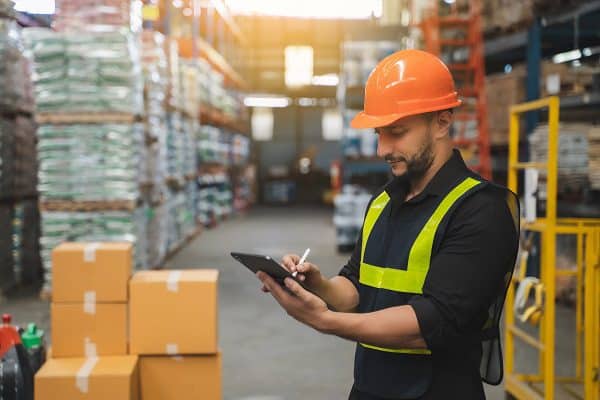
As a pivotal position within the company, the procurement officer coordinates operations according to the constraints of suppliers, the purchasing department, production and logistics. He therefore plays a key role in the smooth running of the company, its profitability and customer satisfaction. Job titles vary according to the scope of the role, the size of the company and its sector of activity: procurement manager, stock manager, procurement and purchasing planning manager, raw materials procurement officer, plant procurement officer, customer procurement officer, etc.
Today's procurement officer carries out his or her duties in an environment where increasingly unstable context. Crises come one after another: health, geopolitical, energy and climate. Shortages, stock-outs, longer delivery times... are at the heart of the news and reveal the strategic role of the procurement officer in maintaining a company's competitive edge.
Knowing how to manage priorities and emergencies is an essential part of the job. But it is above all the ability to adapt to the increasing digitalisation of the supply chain and service rate requirements, which will prove decisive in the years to come. Tomorrow's supplier will be agile and data-driven!
What are the main tasks of a procurement officer?
The supply manager coordinates the flow of products and stocks upstream of the production line or the company's points of sale. Their day-to-day work involves three main tasks.
3 main missions
Within the supply chain, the job of procurement officer is situated between the purchasing and logistics functions.
1/ Defining the company's needs
If you work in close proximity to the purchasing department, you will work with buyers on a daily basis. As such, they take part in negotiations with suppliers. They also contribute to the sourcing of new suppliers. In this case, they are involved upstream in the qualification and listing processes. Above all, they work with the selected suppliers to put in place a supply plan based on the constraints expressed by internal customers (sales outlets and/or factories).
[Note]
In an SME, they may have the dual role of buyer-supplier.
2/ Manage processes and service providers
When they work close to production, supply managers are confronted with the company's logistical problems. First of all, they are responsible for sourcing and selecting any service providers, particularly carriers and forwarding agents. They then supervise supply operations. He plans and coordinates the transport of products or goods: stock management, coherent organisation of flows, management of shipments, etc. His role also includes a legal aspect. As such, they must ensure that the terms of the contract are respected, in particular compliance with deadlines and conformity of the materials or products received. They are also responsible for managing disputes. Finally, he or she controls the financial side of the business, taking care of payments to service providers.
3/ Monitoring supply operations
The Purchaser implements key indicators and dashboards to measure the performance of the actions taken: stock rotation rate, delivery times, availability rate, etc. He analyses the indicators, points out malfunctions, provides solutions and reports to his superiors.
Management of the procurement department
You may be required to manage a team. They define and structure the department's working methods. They may initiate and manage projects to improve and optimise supply processes. Depending on the size of the company, he or she may play an active role in a project to improve and optimise supply processes.automation of the procurement function. In other words, contributing to the emergence of a 4.0 supply chain. This digital and connected supply chain can be supported by a number of tools: RPA (robotised process automation), artificial intelligencedigital twins, machine learning, IoT (Internet of Things) or cloud.
Variations according to business sector, products and company size
The role of the purchasing manager varies greatly depending on the sector of activity and the type of products marketed.
Sector specificities
In industry, the "customer" for procurement teams is production (factory, workshop, etc.). The procurement function is sometimes centralised, sometimes partially or entirely decentralised.
In distribution, the procurement manager relies on supply managers based on the production site. They have a lot of direct contact with production managers. They are also in constant contact with purchasing, marketing and sales teams.
Specific product features
Perishable products: the supplier's tasks are refocused on transport conditions and security of supply.
Products for which the supplier is a long way from the place of production or distribution: this is the case, for example, in low-cost countries. As the supply chain is particularly complex, the procurement officer keeps a close eye on transport operations.
Products manufactured and delivered in large series: the procurement officer concentrates above all on organising the process and computerising it.
[What you need to know]
The day-to-day challenge faced by the supplier is to manage and optimise stocks, guarantee product availability and service levels, while applying the terms and conditions previously negotiated by the purchasing department. In other words: optimising logistics costs while placing orders in accordance with previously agreed constraints.
What training do you need to become a procurement officer?
To become a procurement officer, it's best to have a Bac +2 to Bac +5 diplomas. DUTs, BTSs and masters specialising in logistics and transport are popular with recruiters. Business school courses specialising in logistics or international trade are very popular. General engineers specialising in electronics, mechanics, industrial logistics or production organisation and management are also well placed.
Access to the profession is also possible if you have a solid experience in logistics control, stock management or customer service (minimum 5 years). This experience can be supplemented by professional training in the following areas procurement and stock management techniques.
What skills do you need?
The position primarily requires a very good interpersonal skillsThis is because the procurement officer is in constant contact with both internal and external players. Internally, this enables them to keep abreast of everything that's going on in the company, and in particular to have a good level of information on sales and marketing operations. Externally, being a skilled negotiator is a major asset. Procurement officers must also be able to adapt quickly and cope well with stress. They must be rigorous and have excellent organisational skills.
Skills development in a context of digitalisation
Procurement 4.0 will be based on the use of data. They will therefore have an increasingly data-driven mindset. In fact, the development of digital supply chain management is set to have a major impact on the supply function in the coming years.
The aim? Reduce repetitive administrative tasks as much as possible and free up time for higher added-value tasks. For example: simplify order placement by increasing the proportion of orders that can be automatically renewed. All the way up to 95 %!
For that it is necessary improve demand forecasts. Firstly, this requires the collection of quality data (harmonisation and pooling of data). Secondly, it means analysing large quantities of data. Fortunately, the development of artificial intelligence in the supply chain should make it easier for supply chain managers to do this. But we also need to bear in mind that the availability of digital tools is not everything. So the ultimate challenge for these professionals will be to acquire or perfect their skills in managing and exploiting data. This is the new challenge for supply chain managers!
TECHNICAL SKILLS (hard skills)
- Perfect knowledge of the constraints of the supply chain links (supplier - transport - production - sales)
- Proficiency in supply chain management software
- Mastery of data processing tools
- Fluency in English (professional level) and possibly another foreign language
- Knowledge of customs regulations
BEHAVIOURAL AND RELATIONAL SKILLS (soft skills)
- Ability to analyse and summarise
- Good interpersonal skills, listening skills and negotiating skills
- Very good stress management skills
- Responsive decision-making
How much does a procurement officer earn?
The remuneration and salary progression for a procurement technician vary according to experience. For beginners, the range is €22,000 to €28,000 gross per annum. Experienced candidates can expect to earn between €28,000 and €45,000 gross per annum. The average gross annual salary is around €37,000.
What are its development prospects?
Executives with at least five years' professional experience can progress to the position of supply manager or director. Experienced supply managers can also progress to other positions such as supply chain manager, logistics manager or purchasing manager.
What are the attractions and constraints of being a procurement officer?
- Strong job opportunities
- Many daily challenges
- Numerous internal and external interactions
- Career development prospects
- Hard work: working outdoors, in refrigerators, etc.
- Staggered working hours (subject to deliveries)
- Stress linked to managing unforeseen events and emergencies