Een onderhoudsafdeling repareert wanneer er een storing optreedt. Ja, maar problemen van geval tot geval aanpakken zorgt voor extra kosten, productievertragingen en dus een lagere productiviteit, om nog maar te zwijgen van de vermoeidheid van technici. Industrieel onderhoud speelt daarom een sleutelrol in de economische stabiliteit van de industrie van de toekomst.
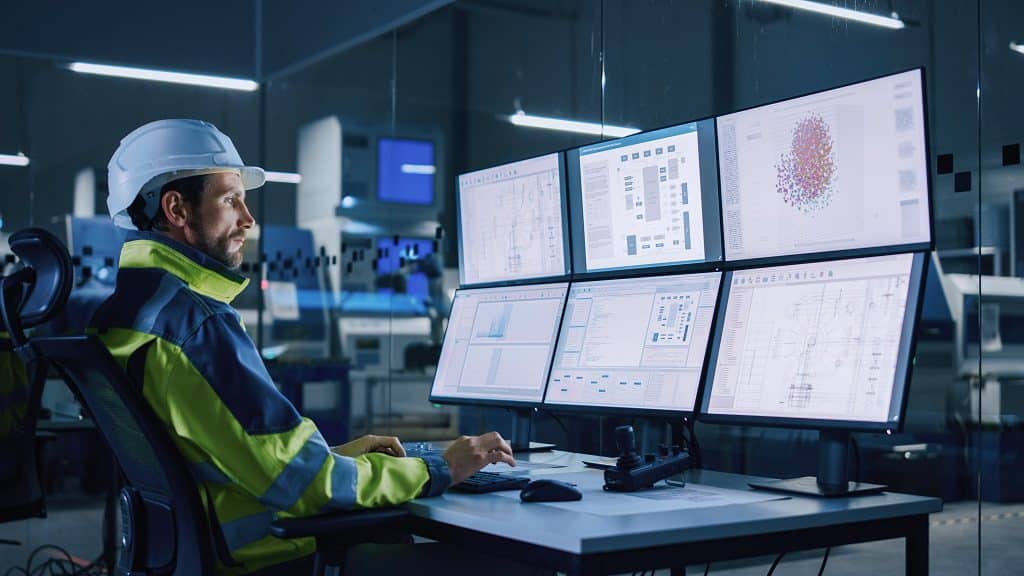
De industrie is een sector die voortdurend in beweging is. En om de stabiliteit en prestaties te garanderen die synoniem staan voor een lange levensduur, is het essentieel voor de industrie om ervoor te zorgen dat haar radertjes goed gesmeerd lopen. Het is daarom essentieel voor de industrie om te streven naar verbetering van de servicekwaliteit, nu en in de toekomst. Daarom speelt onderhoud een sleutelrol in dit proces van prestatieverbetering. Maar hoe kan een onderhoudsafdeling intelligent en effectief worden beheerd? Guy Besson, een expert in de organisatie en betrouwbaarheid van industrieel onderhoud, legt uit hoe je van correctief onderhoud naar preventief onderhoud kunt gaan.
Preventief onderhoud: wat staat er op het spel?
In het belang van de economie en winstgevendheid willen bedrijven snijden in hun budgetten. Maar bezuinigingen (als ze goed doordacht zijn) zijn niet noodzakelijkerwijs nadelig. En het is dit evenwicht dat kenmerkend is voor de uitdagingen waarmee onderhoudsafdelingen worden geconfronteerd, waarvan de budgetten de neiging hebben te exploderen wanneer storingen geval per geval worden aangepakt, zonder een echt diepgaand beleid. Een verlaging van het budget in combinatie met een relevante verbeteringsaanpak kan dus zijn vruchten afwerpen.
Het opstarten van een kostenoptimalisatieproces voldoet aan de QCD-doelstelling: onberispelijke kwaliteit, geoptimaliseerde kosten, deadlines gehaald... door te anticiperen op technische incidenten in plaats van eronder te lijden. Geschat wordt dat onderhoudskosten tot 50 % vertegenwoordigen productiekosten. Een preventieve aanpak zou de kosten en het aantal storingen verlagen, met minder investeringen in nieuwe machines en een effectievere inzet van technici.
Uw preventieve onderhoudsaanpak structureren
Computers, mechanica... alle apparaten, gereedschappen en machines hebben onderhoud nodig. Dit is een vakgebied dat theoretische kennis van de verschillende soorten machines, vaardigheden en technische en pragmatische knowhow combineert, vaak verworven door ervaring. Maar deze door ervaring opgedane kennis heeft over het algemeen één nadeel: ze is vaak moeilijker te structureren op een methodische en overdraagbare manier. Maar elke onderhoudsaanpak vereist een methodische aanpak.
De acht hoofdzaken van onderhoud
Deze benodigdheden zorgen voor een bijna naadloze organisatie en zijn de eerste stap naar een georganiseerde service:
- een uitrustingsmatrix geproduceerd en gebruikt ;
- efficiënt gebruik van hulpbronnen (technici, gereedschap, leveranciers);
- reserveonderdelen gesorteerd en gecodeerd zodat je ze in minder dan 1 minuut kunt vinden;
- uitgevoerde storingsanalyses (met behulp van de juiste hulpmiddelen om de oorzaak van storingen te begrijpen);
- het opzetten van goede controle-indicatoren;
- machines onder toezicht smeren en legen ;
- Opstellen van procedures voor alle onderhoudsacties en -processen die door de afdeling worden uitgevoerd (acties, nomenclaturen, organisatie, enz.);
- documentatie die georganiseerd en direct beschikbaar is.
Twee pijlers om deze benodigdheden te structureren
Volgens onze expert gaat de dynamiek die wordt gegenereerd door deze acht essentiële zaken gepaard met twee pijlers die niet mogen worden verwaarloosd als het gaat om het optimaliseren van middelen.
De eerste pijler is de matrix die bestaat uit de acht hoofdzaken. Het classificeren van machines (volgens verschillende criteria die specifiek zijn voor de activiteit) maakt het in feite mogelijk om een lijst in volgorde van kriticiteit te verkrijgen. Zo weet je welke machines het meeste "risico" lopen, of welke prioriteit hebben wat betreft diepgaand onderhoudswerk.
De tweede pijler is de 80/20-regel. Dit betekent dat 80% van de risico's geconcentreerd zijn op 20% van de machines die het meeste risico lopen. Deze regel maakt een duurzamer onderhouds- en herstelbeleid mogelijk, waarbij het risico op storingen wordt beperkt en het gebruik van al deze middelen (gereedschap, personeel, enz.) wordt geoptimaliseerd.
Het belangrijkste is om je bewust te zijn van deze factoren om de werklast te verminderen en te voorkomen dat je wordt overweldigd door vermijdbare storingen.
De vijf oorzaken van pech onder de knie krijgen
Of het nu gaat om redenen van organisatie, verantwoordelijkheid of vaardigheden, reparaties zijn niet langer voldoende in een omgeving die concurrentievermogen eist. Herhaalde storingen aan dezelfde machine verminderen het potentieel voor winstgevendheid aanzienlijk. Inzicht in de oorzaak van een storing is daarom van fundamenteel belang. Op het gebied van onderhoud is het zelfs de basis van goed werk. Als je de oorzaak van een storing kent, kun je een oplossing vinden en zo een deel van de risico's beheersen.
- onjuist gebruik van apparatuur: te snel, te hard, met het verkeerde materiaal, enz.
- slecht onderhoud van de machine: dit is de verantwoordelijkheid van de gebruiker, die de machine moet schoonmaken, slijtage moet opmerken, enz.
- onvoldoende onderhoud: een onderdeel niet op tijd vervangen, olie te laat ververst, enz.
- de menselijke factor: wordt vaak gelijkgesteld aan een vaardigheidsprobleem, maar kan ook een kwestie zijn van een slecht uitgevoerde reparatie, verstrooidheid, enz.
- een ontwerpfout.
"Voor elk probleem is er een oplossing", en dat is precies wat deze analyse doet. Een goed begrip van een storing is de sleutel tot adequate onderhoudsmiddelen.
Probleemoplossing begrijpen
Er zijn drie belangrijke stadia in het oplossen van problemen:
- het probleem vormen;
- zoek naar de belangrijkste oorzaken ;
- het actieplan lanceren.
Zodra de diagnose is gesteld, moet er een effectieve en passende oplossing worden gevonden. Met andere woorden, een oplossing die overeenkomt met de noodzakelijke investering die kan worden gedaan (tijd, budget, middelen, enz.) binnen de grenzen van wat kosteneffectief is en die de onderhoudsafdeling in staat stelt effectief te zijn. Drie hulpmiddelen kunnen aan deze behoefte voldoen:
- JDI: "just do it" is relevant voor kleine problemen die binnen een uur kunnen worden opgelost, zonder hiërarchische validatie, zonder gereedschap te bestellen, etc. Een probleem dat in een uur is opgelost door een technicus is hier een voorbeeld van. Een probleem in 1 uur opgelost door een technicus.
- De MARP of Snelle Kaizen-methode: het verbeteringswiel, afgeleid van lean management, combineert verschillende probleemoplossende analyse- en planningstools (QQOQCCP, de 5 waaroms, het Ishikawa-diagram). Het kan het begin zijn van een actieplan en is daarom meer geschikt voor diepgewortelde of repetitieve onderhoudsproblemen. Deze methode is van toepassing op problemen van gemiddelde complexiteit: 1 tot 2 dagen voor één of twee technici.
- 8D (D voor discipline, d.w.z. "te ondernemen actie"): dit is een analysemethode in 8 stappen die de besluitvorming structureert in een continu verbeteringsproces. De verschillende stappen houden rekening met alle facetten van het op te lossen probleem en doen vooral een beroep op de samenwerkingsgeest. Deze meer gestructureerde methode is meer geschikt voor complexere problemen waarbij verschillende resources betrokken zijn (kwaliteitsafdeling, ontwerpbureau, enz.), met drie tot vijf personen en een langere planningshorizon (ongeveer 1 tot 4 maanden).
Het organiseren van de afhandeling van storingen maakt de weg vrij voor "nul storingen" door de aanpak te structureren en een volledige analyse van een probleem te vereisen om een blijvend antwoord te kunnen bieden.
Focus op training
Door een gebrek aan tijd en perspectief werken onderhoudsafdelingen meestal op basis van just-in-time, correctief onderhoud. Om echte besparingen te realiseren en een aantrekkelijk rendement op investering te behalen, moeten bedrijven echter overstappen op een preventieve onderhoudsaanpak.
Training De TPM-pijler inzetten: gepland onderhoud behandelt de verschillende hulpmiddelen voor preventief onderhoud, waarbij altijd wordt uitgegaan van de beroepservaring van de deelnemers. Door gepersonaliseerde diagnoses te stellen en collectieve intelligentie te gebruiken, willen we de deelnemers helpen om een methodische analyse van hun storingen uit te voeren en een actieplan op te stellen dat relevant is voor hun bedrijf en hun machines en aan hun behoeften voldoet. En dat is waar het in ons programma om draait: weten hoe je deze verschillende tools kunt aanpassen om storingen op te lossen en tegelijkertijd leren hoe je HET actieplan opstelt dat het bedrijf geld zal besparen.
Preventief onderhoud heeft alles in zich om de industrie te helpen de prestaties en winstgevendheid te verbeteren. Dankzij de juiste methoden en hulpmiddelen zullen investeringen snel effect hebben op het personeel (en hun motivatie) en op de levensduur van machines. En last but not least zal dit onderhoudsbeleid mee evolueren met de industrie, waarbij met name de technologische vooruitgang het in sommige gevallen mogelijk maakt om een voorspellend onderhoudsbeleid te implementeren.