Leanmanagement en Six Sigma® zijn verbetermethodologieën waar je waarschijnlijk al van gehoord hebt. In feite zijn ze essentieel geworden in bedrijven in het algemeen en in de industrie in het bijzonder. Tussen de zoektocht naar optimalisatie en de behoefte aan efficiëntie, hebben bedrijven er alle belang bij om nieuwe benaderingen te ontwikkelen die gericht zijn op prestaties op alle productieniveaus. Terwijl we de belangrijkste principes van Lean en Six Sigma in herinnering brengen®, Industrie-expert Frédéric Rouzeau laat ons zien hoe ze elkaar aanvullen en nauw verbonden zijn met Industrie 4.0.
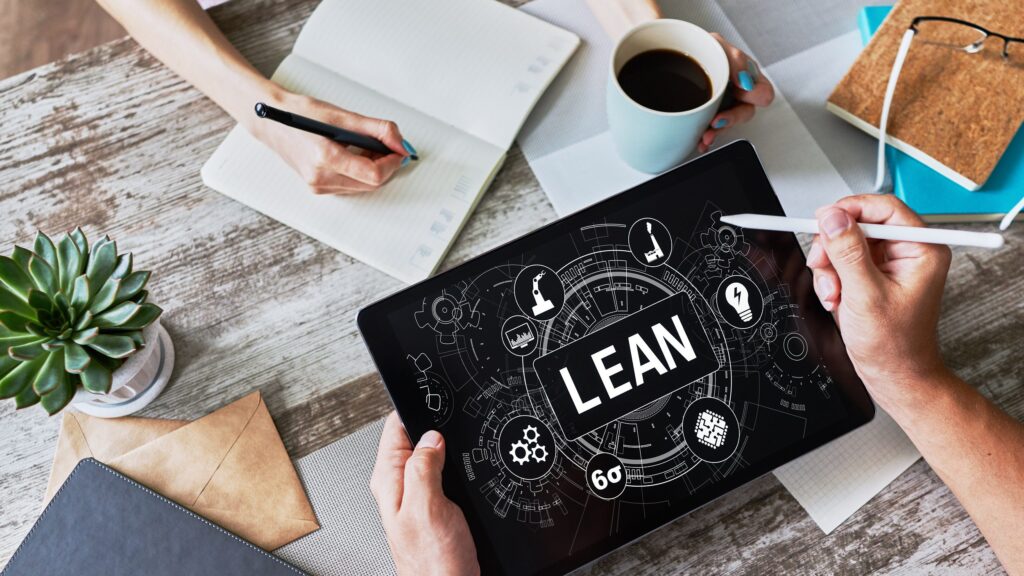
De Lean methode: oorsprong en principes
In de jaren 1950 implementeerde Taiichi Ohno, de industriële directeur van Toyota, het Toyota Productie Systeem (TPS), een nieuwe manier om industriële activiteiten te beheren. Het belangrijkste doel was om alle activiteiten elimineren die geen waarde toevoegen voor klanten.
In het begin van de jaren 1980 bestudeerde een team van MIT-onderzoekers onder leiding van James P. Womack het succes van Toyota. Ze raakten er al snel van overtuigd dat Toyota's TPS in alle bedrijven, in alle sectoren en in alle landen kon worden toegepast. Ze besloten deze nieuwe aanpak "lean" te noemen, een term die perfect deze obsessieve jacht op de verschillende vormen van verspilling binnen processen illustreert.
In 1991 publiceerden James Womack en twee andere MIT-onderzoekers De machine die de wereld veranderde (Harper Collins, 1991), waarin hun conclusies van het onderzoek naar Toyota's TPS worden gepresenteerd. Dit boek draagt bij aan de inzet van slanke productie Het is nog steeds de maatstaf voor industrieel management. Lean management heeft zich sindsdien wijd verspreid over alle activiteitensectoren (industrie, diensten, kantoren, gezondheid, enz.).
Lean management: een wereldwijde visie op de industrie
Dit type management is gebaseerd op de sterke betrokkenheid van al het personeel. Ze worden gemobiliseerd in teams om verbeteringen te identificeren en voor te stellen die gericht zijn op het elimineren van verspilling. Afval kan drie verschillende vormen aannemen, afhankelijk van de aard ervan:
- Muri: de verzadiging van een bron, een taak die buitensporig, te moeilijk of zelfs onmogelijk is;
- Mura: onregelmatigheden, variabiliteit ;
- Muda: taken zonder toegevoegde waarde. Deze kunnen worden onderverdeeld in acht verschillende soorten:
- overproductie (te veel of te snel produceren): de ergste van allemaal omdat het alle andere genereert;
- onnodige voorraden;
- onnodig transport en handling (van producten);
- overbewerking (overbodige bewerkingen, overkwaliteit) ;
- onnodige verplaatsingen en reizen (door werknemers) ;
- fouten, defecten en afkeuringen ;
- wachttijden en vertragingen ;
- onderbenutting van vaardigheden.
De Six Sigma® methode: oorsprong en principes
De Six Sigma® methode is iets recenter. Het ontstond aan het eind van de jaren 1980 toen Bill Smith, een ingenieur bij Motorola, het ontwikkelde om productieprocessen en de kwaliteit van hun producten te verbeteren. Het doel was om de klanttevredenheid te verbeteren. De methode werd beroemd in de jaren 90, dankzij General Electric en haar charismatische voorzitter Jack Welch. Hij was het die besloot om de methode te verbeteren en toe te passen in de hele GE-groep, met doorslaand succes.
De Six Sigma® methode is gericht op procesvariabiliteit verminderen om het risico dat het product (of de dienst) wordt afgekeurd door de ontvanger te elimineren of te verminderen onder het voorwendsel dat het niet aan de verwachtingen of specificaties voldoet. Deze methode vertrouwt voornamelijk op statistische hulpmiddelen om de parameters product of proces. Het wordt ingezet in projectmodus, gemanaged door een Green of Black Belt gecertificeerde projectmanager. Het is gestructureerd in vijf verschillende fasen: Definieer, Meet, Analyseer, Verbeter, Controleer, of DMAIC.
Elke fase van het DMAIC-project heeft specifieke doelstellingen en maakt gebruik van verschillende hulpmiddelen:
- Definieer Deze omvatten de omkadering van het project, het identificeren van operationele en financiële voordelen, het begrijpen van de verwachtingen van de klant en CTQ's (critical to quality), ook bekend als Yi, het in kaart brengen van het proces, enz;
- Meeteenheid Maak een lijst van de potentieel invloedrijke factoren in het proces (Xi genoemd) en meet Yi en Xi tegelijkertijd nadat de betrouwbaarheid van de meetprocessen is gegarandeerd;
- Analyseren Voer een gegevensanalyse uit om de Xi-factoren te identificeren die de grootste invloed hebben op de Yi (antwoorden);
- verbeteren Zoek manieren om de meest invloedrijke Xi te verbeteren;
- Controleer hulpmiddelen voor procesbeheer zoals statistische procescontrole (SPC).
Lean-Six Sigma®
Met hun belangrijkste gemeenschappelijke punt (klantgerichtheid) werden de twee methodologieën begin jaren 2000 gecombineerd tot Lean-Six Sigma® (LSS). De twee benaderingen vullen elkaar enorm aan:
Karig
- praktisch en pragmatisch
- stroomoriëntatie
- verspilling elimineren
- Verbeteren door organisatie (betrokkenheid)
- voortdurende verbetering (dagelijks)
- procesverbetering
Six Sigma®
- analytisch en statistisch
- kwaliteitsoriëntatie
- activiteiten met toegevoegde waarde verbeteren
- verbetering van de organisatie
- ontwrichtende verbetering (projectmodus)
- procesverbetering
Maar hoe kan deze combinatie van methoden in de praktijk worden toegepast op het gebied van Industrie 4.0? Wat zijn de specifieke kenmerken van dit gebied die ze bijzonder relevant maken?
Industrie 4.0
L'industrie 4.0Digitalisering, ook vaak de "connected factory" genoemd, markeert de vierde industriële revolutie, volgend op mechanisering (1.0), massaproductie (2.0) en automatisering (3.0). Dankzij digitalisering wordt de industrie een onderling verbonden wereldwijd systeem. Geordend in technologische bouwstenen hebben de vele innovaties een directe of indirecte impact op alle industriefuncties. Hier volgen enkele voorbeelden van de meest voorkomende bouwstenen:
- Efficiënte processen (geavanceerde machinale bewerking, additieve productie, enz;)
- automatisering, behandelingssystemen ;
- productgegevens meten en analyseren (realtime aangesloten sensoren, enz.);
- Communicerende werkstations en machines (verbonden operator, augmented reality, MES (Manufacturing Execution System), intelligente en collaboratieve machines, enz;)
- digitale mock-up (product-/processimulatie, digitale mock-up, digitale tweeling, virtuele realiteit, enz;)
- de predictief onderhoudaangesloten machineonderhoud ;
- sturen en beheren van het bedrijf (samenwerken, workflow/EDM (elektronisch documentbeheer), enz.)
Wat zijn de verbanden tussen Lean, Six Sigma® en Industry 4.0?
Het is ondenkbaar om een technologische bouwsteen te implementeren zonder eerst een sterke cultuur van lean binnen het bedrijf. Dit komt doordatzelfs als het geautomatiseerd is, blijft afval afval. Dit geldt in het bijzonder voor behandeling en opslag.
Omgekeerd zullen bepaalde bouwstenen aanzienlijk bijdragen aan het versterken van de Lean methode. Hier volgen enkele voorbeelden:
- Augmented reality: het kan fouten voorkomen of opsporen;
- real-time prestatiebeheer ;
- communicerende machines en aangesloten operators: ze vereenvoudigen de bewaking en traceerbaarheid;
- Robotica en geautomatiseerde goederenbehandeling: ze verminderen het werk;
- training van operators met behulp van virtuele of augmented reality;
- toegankelijkheid en betrouwbaarheid van werkdocumenten dankzij EDM.
Wat betreft Six Sigma® ligt de link met MES, intelligente en samenwerkende machines, voorspellend onderhoud, efficiënte processen, etc. voor de hand, omdat het identificeren en bewaken van belangrijke parameters essentieel lijkt. Het is daarom zeer waarschijnlijk dat oplossingen van het 4.0-type worden overwogen tijdens de DMAIC-verbeteringsfase.
Door 'moderne' technologische hulpmiddelen en processen te gebruiken, is Industrie 4.0 een perfecte voedingsbodem voor de toepassing van Lean Six Sigma® en zijn zoektocht om het overbodige uit te bannen. Door elke productiefase te analyseren met behulp van de DMAIC-methodologie zet Industrie 4.0 zich bovendien volledig in voor optimalisatie.
Dus aan de ene kant hebben we een aanpak die gericht is op de systematische verbetering van processen (Lean) en aan de andere kant een methode die als doel heeft om alle vormen van variatie te verminderen (Six Sigma®). Door deze twee concepten te combineren, maakt Lean Six Sigma® de continue verbetering van processen mogelijk, waarbij de klant centraal staat, en is het een duidelijke weg naar uitmuntendheid. Lean Six Sigma® maakt echter deel uit van een kwaliteitsaanpak die alleen kan werken en standhouden met steun van het management en een sterk bewustzijn onder werknemers. Met andere woorden, Industrie 4.0 kan niet zonder een meer samenwerkende organisatie en training voor de belangrijkste spelers in het project.