Gestión ajustada y Six Sigma® son metodologías de mejora de las que probablemente ya haya oído hablar. De hecho, se han convertido en esenciales en las empresas en general y en la industria en particular. Entre la búsqueda de optimización y la necesidad de eficacia, las empresas tienen todo el interés en desarrollar nuevos enfoques orientados al rendimiento en todos los niveles de producción. Recordando los grandes principios de Lean y Six Sigma®, El experto del sector Frédéric Rouzeau nos muestra cómo se complementan y están estrechamente vinculadas a la Industria 4.0.
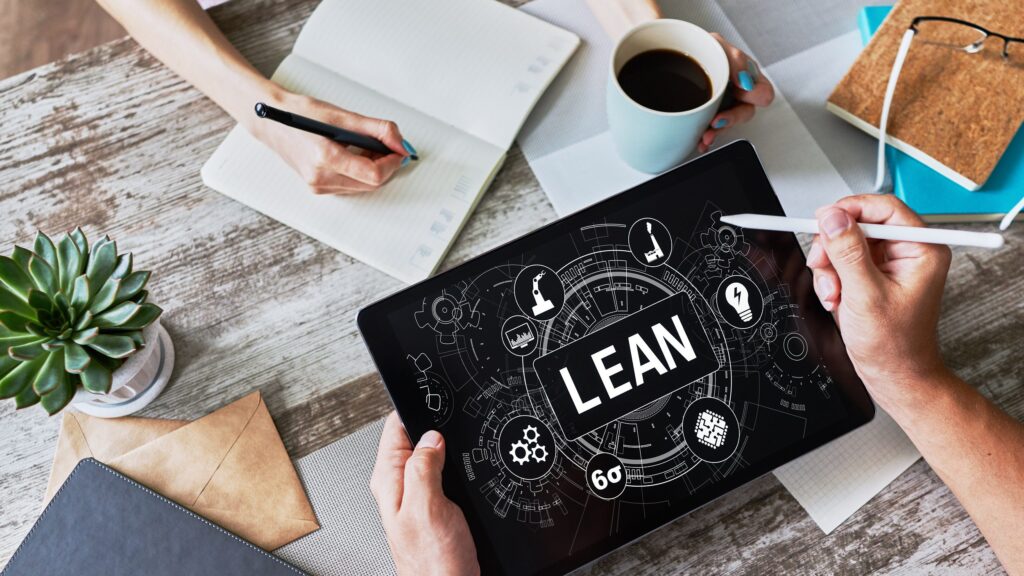
El método Lean: orígenes y principios
En los años 50, Taiichi Ohno, director industrial de Toyota, implantó el Sistema de Producción Toyota (TPS), una nueva forma de gestionar las actividades industriales. Su principal objetivo era eliminar cualquier actividad que no aporte valor añadido a los clientes.
A principios de los años 80, un equipo de investigadores del MIT dirigido por James P. Womack estudió el éxito de Toyota. Rápidamente se convencieron de que el TPS de Toyota podía aplicarse en todas las empresas, en todos los sectores y en todos los países. Decidieron llamar a este nuevo enfoque "lean", un término que ilustra perfectamente esta búsqueda obsesiva de las distintas formas de despilfarro dentro de los procesos.
En 1991, James Womack y otros dos investigadores del MIT publicaron La máquina que cambió el mundo (Harper Collins, 1991), que presenta sus conclusiones del estudio del TPS de Toyota. Este libro contribuye al despliegue de fabricación ajustada Sigue siendo la referencia de la gestión industrial. Desde entonces, la gestión ajustada se ha extendido ampliamente a todos los sectores de actividad (industria, servicios, oficinas, sanidad, etc.).
Lean management: una visión global de la industria
Este tipo de gestión se basa en una fuerte implicación de todo el personal. Se movilizan en equipos para identificar y proponer mejoras destinadas a eliminar los residuos. Los residuos pueden adoptar tres formas diferentes según su naturaleza:
- Muri: la saturación de un recurso, una tarea excesiva, demasiado difícil o incluso imposible;
- Mura: irregularidades, variabilidad ;
- Muda: tareas sin valor añadido. Pueden dividirse en ocho tipos diferentes:
- sobreproducción (producir demasiado o demasiado pronto): la peor de todas porque genera todas las demás;
- existencias innecesarias;
- transporte y manipulación innecesarios (de productos);
- sobreprocesamiento (operaciones superfluas, exceso de calidad) ;
- desplazamientos y viajes innecesarios (de los empleados) ;
- errores, defectos y rechazos ;
- tiempo de espera y retrasos ;
- infrautilización de las competencias.
El método Six Sigma®: orígenes y principios
El método Six Sigma ® es algo más reciente. Se originó a finales de los años 80, cuando Bill Smith, un ingeniero de Motorola, lo desarrolló para mejorar los procesos de fabricación y la calidad de sus productos. El objetivo era mejorar la satisfacción del cliente. El método se hizo famoso en los años 90, gracias a General Electric y a su carismático presidente Jack Welch. Fue él quien decidió mejorarlo y aplicarlo en todo el grupo GE con un éxito rotundo.
El método Six Sigma® tiene como objetivo reducir la variabilidad del proceso para eliminar o reducir el riesgo de que el producto (o servicio) sea rechazado por su destinatario. con el pretexto de que no cumple las expectativas o las especificaciones. Este método se basa principalmente en herramientas estadísticas para identificar y controlar los parámetros producto o proceso. Se despliega en modo proyecto, dirigido por un gestor de proyectos certificado Green o Black Belt. Se estructura en cinco fases distintas: Definir, Medir, Analizar, Mejorar y Controlar, o DMAIC.
Cada etapa del proyecto DMAIC tiene objetivos específicos y utiliza herramientas diferentes:
- Defina Entre otras cosas, hay que enmarcar el proyecto, identificar las ventajas operativas y financieras, comprender las expectativas del cliente y las CTQ (críticas para la calidad), también conocidas como Yi, trazar el proceso, etc;
- Medir Enumerar los factores potencialmente influyentes en el proceso (denominados Xi) y medir simultáneamente Yi y Xi tras garantizar la fiabilidad de los procesos de medición;
- Analizar Realiza un análisis de los datos para identificar los factores Xi que más influyen en el Yi (respuestas);
- Mejorar Encontrar formas de mejorar el Xi más influyente;
- Consulte Herramientas de gestión de procesos, como el control estadístico de procesos (CEP).
Lean-Seis Sigma
Con su principal punto en común (la orientación al cliente), ambas metodologías se combinaron a principios de la década de 2000 para dar lugar a Lean-Six Sigma® (LSS). Ambos enfoques se complementan enormemente:
Inclinarse
- práctico y pragmático
- orientación del flujo
- eliminar residuos
- Mejorar mediante la organización (implicación)
- mejora continua (día a día)
- mejora de los procesos
Seis Sigma
- analítico y estadístico
- orientación hacia la calidad
- mejorar las actividades de valor añadido
- mejorar la organización
- mejora disruptiva (modo proyecto)
- mejora de los procesos
Pero, ¿cómo puede aplicarse en la práctica esta combinación de métodos en el ámbito de la Industria 4.0? Cuáles son las características específicas de este ámbito que los hacen especialmente pertinentes?
Industria 4.0
Laindustria 4.0La digitalización, también llamada con frecuencia "fábrica conectada", marca la cuarta revolución industrial, tras la mecanización (1.0), la producción en masa (2.0) y la automatización (3.0). Gracias a la digitalización, la industria se está un sistema mundial interconectado. Organizadas en bloques tecnológicos, las numerosas innovaciones tienen un impacto directo o indirecto en todas las funciones de la industria. He aquí algunos ejemplos de los componentes más frecuentes:
- Procesos eficientes (mecanizado avanzado, fabricación aditiva, etc.);
- automatización, sistemas de manipulación ;
- medición y análisis de los datos del producto (sensores conectados en tiempo real, etc.);
- Puestos de trabajo y máquinas comunicados (operador conectado, realidad aumentada, MES (Manufacturing Execution System), máquinas inteligentes y colaborativas, etc.);
- maqueta digital (simulación de producto/proceso, maqueta digital, gemelo digital, realidad virtual, etc.);
- el mantenimiento predictivomantenimiento de máquinas conectadas ;
- dirección y gestión de la empresa (trabajo en colaboración, flujo de trabajo/EDM (gestión electrónica de documentos), etc.).
¿Cuáles son los vínculos entre Lean, Six Sigma® e Industria 4.0?
Es impensable desplegar un ladrillo tecnológico sin contar antes con una sólida cultura de inclinarse dentro de la empresa. Esto se debe a queaunque estén automatizados, los residuos siguen siendo residuos. Esto se aplica en particular a la manipulación y el almacenamiento.
A la inversa, ciertos elementos constitutivos contribuirán significativamente a reforzar el método Lean. He aquí algunos ejemplos:
- Realidad aumentada: puede prevenir o detectar errores;
- gestión del rendimiento en tiempo real ;
- máquinas comunicadas y operarios conectados: simplifican el seguimiento y la trazabilidad;
- Robótica y manipulación automatizada de materiales: reducen el trabajo pesado;
- formación de operadores mediante realidad virtual o aumentada;
- accesibilidad y fiabilidad de los documentos de trabajo gracias a EDM.
En lo que respecta a Six Sigma®, el vínculo con MES, máquinas inteligentes y colaborativas, mantenimiento predictivo, procesos eficientes, etc. es evidente, ya que la identificación y el seguimiento de los parámetros clave parecen esenciales. Por tanto, es muy probable que las soluciones de tipo 4.0 se tengan en cuenta durante la fase de mejora DMAIC.
Al adoptar herramientas y procesos tecnológicos "modernos", la Industria 4.0 es un caldo de cultivo perfecto para la aplicación de Lean Six Sigma® y su búsqueda de la erradicación de lo superfluo. Además, al analizar cada etapa de la producción mediante la metodología DMAIC, la Industria 4.0 se compromete plenamente con la optimización.
Así pues, por un lado tenemos un enfoque orientado a la mejora sistemática de los procesos (Lean) y, por otro, un método cuyo objetivo es reducir todas las formas de variación (Six Sigma®). Combinando estos dos conceptos, Lean Six Sigma® permite la mejora continua de los procesos, situando al cliente en el centro de las preocupaciones, y constituye una vía clara hacia la excelencia. Sin embargo, Lean Six Sigma® forma parte de un enfoque de calidad que sólo puede funcionar y perdurar con el apoyo de la dirección y una fuerte concienciación de los empleados. En otras palabras, la Industria 4.0 no puede prescindir de una organización más colaborativa y de la formación de los actores clave del proyecto.