Un departamento de mantenimiento repara cuando se produce una avería. Sí, pero gestionar los problemas caso por caso genera costes adicionales, retrasos en la producción y, en consecuencia, una menor productividad, por no hablar de la fatiga de los técnicos. Por tanto, el mantenimiento industrial tiene una papel en la estabilidad económica de la industria del futuro.
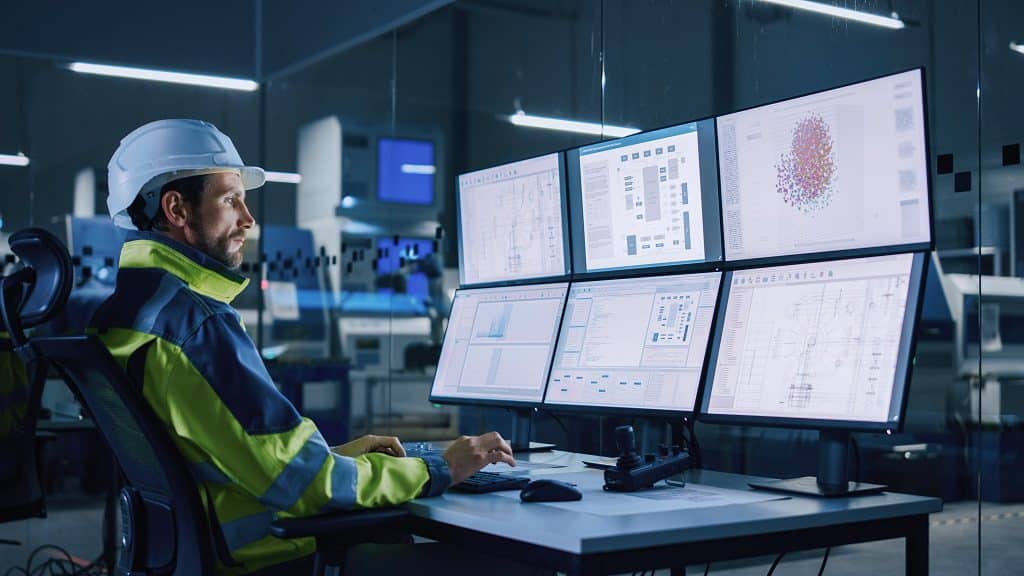
La industria es un sector en constante evolución. Y para garantizar la estabilidad y el rendimiento que son sinónimos de longevidad, es vital que la industria se asegure de que sus ruedas están bien engrasadas. Por tanto, es esencial que la industria trate de mejorar su calidad de servicio ahora y en el futuro. Por ello, el mantenimiento desempeña un papel clave en este proceso de mejora del rendimiento. Pero, ¿cómo gestionar un departamento de mantenimiento de forma inteligente y eficaz? Guy Besson, experto en organización y fiabilidad del mantenimiento industrial, explica cómo pasar del mantenimiento correctivo al mantenimiento preventivo.
Mantenimiento preventivo: ¿qué está en juego?
En aras de la economía y la rentabilidad, las empresas buscan recortar presupuestos. Sin embargo, los recortes presupuestarios (cuando están bien pensados) no son necesariamente penalizadores. Y es este equilibrio el que caracteriza los retos a los que se enfrentan los departamentos de mantenimiento, cuyos presupuestos tienden a dispararse cuando las averías se gestionan caso por caso, sin una verdadera política de fondo. Así pues, un recorte presupuestario acompañado de un enfoque de mejora pertinente puede dar sus frutos.
Poner en marcha un proceso de optimización de costes responde al objetivo QCD: calidad irreprochable, costes optimizados, cumplimiento de los plazos... anticipándose a las incidencias técnicas en lugar de sufrirlas. Se calcula que los costes de mantenimiento pueden representan hasta 50 % costes de producción. Un planteamiento preventivo reduciría los costes y el número de averías, con una menor inversión en nuevas máquinas y una movilización más eficaz de los técnicos.
Estructuración del mantenimiento preventivo
Informática, mecánica... todos los aparatos, herramientas y máquinas requieren mantenimiento. Se trata de un campo que combina conocimientos teóricos sobre los distintos tipos de máquinas, competencias y conocimientos técnicos y pragmáticos, a menudo adquiridos a través de la experiencia. Pero estos conocimientos adquiridos a través de la experiencia suelen tener un inconveniente: a menudo son más difíciles de estructurar de forma metódica y transferible. Pero cualquier planteamiento de mantenimiento requiere un enfoque metódico.
Los ocho elementos esenciales del mantenimiento
Estos elementos esenciales garantizan una organización casi perfecta y son el primer paso hacia un servicio organizado:
- una matriz de equipos producidos y utilizados ;
- eficiencia de los recursos (técnicos, herramientas, proveedores);
- piezas de repuesto clasificadas y codificadas para que pueda encontrarlas en menos de 1 minuto;
- realización de análisis de averías (utilizando las herramientas adecuadas para comprender el origen de las averías);
- el establecimiento de buenos indicadores de seguimiento;
- lubricación y vaciado de máquinas bajo supervisión ;
- Elaborar procedimientos para todas las acciones y procesos de mantenimiento realizados por el departamento (acciones, nomenclaturas, organización, etc.);
- documentación organizada y fácilmente disponible.
Dos pilares para estructurar estos elementos esenciales
Según nuestro experto, la dinámica generada por estos ocho elementos esenciales va acompañada de dos pilares que no se pueden descuidar a la hora de optimizar los recursos.
El primer pilar es la matriz contenida en los ocho elementos esenciales. En efecto, la clasificación de las máquinas (según distintos criterios propios de la actividad) permite obtener una lista por orden de criticidad. Así se sabe qué máquinas son las más "de riesgo", o las que tienen prioridad en términos de trabajos de mantenimiento en profundidad.
El segundo pilar es la regla 80/20. En otras palabras, 80% de los riesgos se concentran en 20% de las máquinas más expuestas. Esta regla permite una política de mantenimiento y restauración más sostenida, limitando el riesgo de avería y optimizando el uso de todos estos recursos (herramientas, personal, etc.).
La clave está en ser consciente de estos factores para reducir la carga de trabajo y evitar verse desbordado por averías evitables.
Dominar las cinco causas de las averías
Ya sea por razones de organización, responsabilidad o competencias, las reparaciones ya no son suficientes en un entorno que exige competitividad. Las averías repetidas en una misma máquina reducen considerablemente el potencial de rentabilidad. Comprender la causa de una avería es, por tanto, fundamental. En el ámbito del mantenimiento, es incluso la base de un trabajo bien hecho. De hecho, conocer la causa de una avería permite encontrar una solución y, por tanto, controlar parte de los riesgos.
- uso incorrecto del equipo: demasiado rápido, demasiado alto, con el material equivocado, etc.
- mantenimiento deficiente de la máquina: es responsabilidad del usuario, que debe ocuparse de limpiarla, advertir el desgaste, etc.
- mantenimiento inadecuado: una pieza no cambiada a tiempo, un cambio de aceite tardío, etc.
- el factor humano: a menudo asimilado a un problema de competencias, puede tratarse de una reparación mal realizada, un despiste, etc.
- un fallo de diseño.
"Hay una solución para cada problema", y eso es exactamente lo que hace este análisis. Comprender bien una avería es la clave para disponer de los recursos de mantenimiento adecuados.
Comprender la resolución de problemas
Hay tres etapas clave en la resolución de problemas:
- plantean el problema;
- buscar las causas clave ;
- poner en marcha el plan de acción.
Una vez realizado el diagnóstico, hay que encontrar una solución eficaz y adecuada. Es decir, una que corresponda a la inversión necesaria que se puede realizar (tiempo, presupuesto, recursos, etc.) dentro de los límites de lo rentable y permita al departamento de mantenimiento ser eficaz. Tres herramientas pueden responder a esta necesidad:
- JDI: "just do it" es pertinente para pequeños problemas que pueden resolverse en una hora, sin validación jerárquica, sin pedir herramientas, etc. Un problema resuelto en una hora por un técnico es un ejemplo. Un problema resuelto en una hora por un técnico.
- El método MARP o Quick Kaizen: la rueda de mejora, derivada del lean management, combina varias herramientas de análisis y planificación de la resolución de problemas (QQOQCCP, los 5 porqués, el diagrama de Ishikawa). Puede ser el inicio de un plan de acción y, por tanto, es más adecuado para problemas de mantenimiento arraigados o repetitivos. Este método se aplica a problemas de complejidad media: de 1 a 2 días para uno o dos técnicos.
- 8D (D de disciplina, es decir, "acción a realizar"): se trata de un método de análisis en 8 etapas que estructura la toma de decisiones como parte de un proceso de mejora continua. Sus distintas etapas permiten tener en cuenta todas las facetas del problema y, sobre todo, requieren un enfoque colaborativo. Más estructurado, es más adecuado para problemas más complejos en los que intervienen distintos recursos (departamento de calidad, oficina de diseño, etc.), con entre tres y cinco personas y un periodo de planificación más largo (de 1 a 4 meses aproximadamente).
Organizar el tratamiento de las averías allana el camino hacia las "cero averías" al estructurar el planteamiento y exigir un análisis completo de un problema para dar una respuesta duradera.
Centrarse en la formación
Debido a la falta de tiempo y perspectiva, los departamentos de mantenimiento suelen trabajar sobre la base del mantenimiento correctivo "justo a tiempo". Sin embargo, para conseguir un ahorro real y un retorno de la inversión atractivo, las empresas deben cambiar a un enfoque de mantenimiento preventivo.
Formación Despliegue del pilar TPM: mantenimiento planificado aborda las distintas herramientas de mantenimiento preventivo, basándose siempre en la experiencia profesional de los participantes. Mediante la elaboración de diagnósticos personalizados y la utilización de la inteligencia colectiva, pretendemos ayudar a los participantes a realizar un análisis metódico de sus averías y a elaborar un plan de acción adaptado a su empresa y a sus máquinas y que responda a sus necesidades. Y en eso consiste nuestro programa: en saber adaptar estas diferentes herramientas a la resolución de problemas, aprendiendo al mismo tiempo a planificar EL plan de acción que permitirá ahorrar dinero a la empresa.
El mantenimiento preventivo lo tiene todo para ayudar a la industria a mejorar su rendimiento y rentabilidad. Gracias a métodos y herramientas apropiados, las inversiones tendrán rápidamente un efecto sobre la mano de obra de los equipos (y su motivación), así como sobre la vida útil de las máquinas. Por último, pero no por ello menos importante, esta política de mantenimiento está llamada a evolucionar a medida que evoluciona la industria, y en particular los avances tecnológicos permiten en algunos casos aplicar una política de mantenimiento predictivo.