Flexible, lightweight, easy to program and, above all, less expensive than conventional robots, the cobots are gaining in popularity, particularly in SMEs. These robots assist humans with repetitive or dangerous tasks: transporting loads, sorting, packing, assembling, measuring and analysing... Meet these versatile, tireless workers.
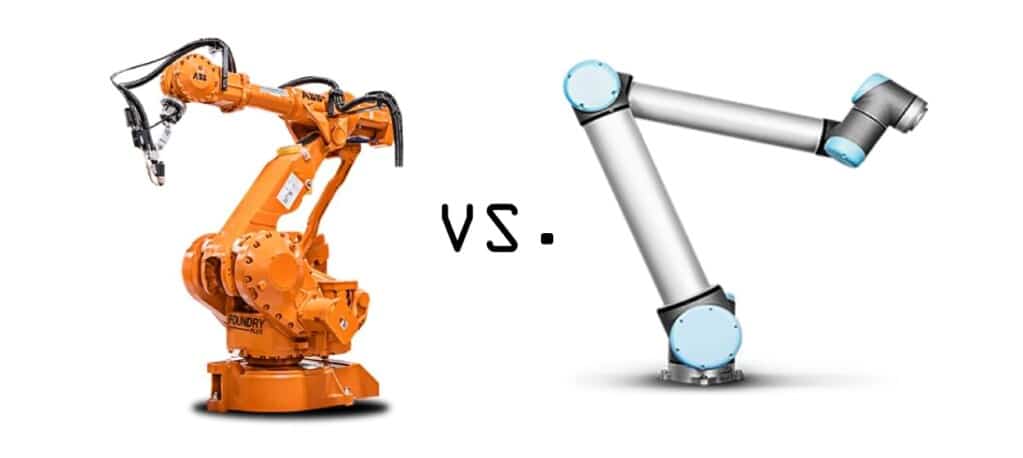
Robots are not in the doldrums. France has never had so many robots in its factories. The year 2022 saw a record 13 % growth in the number of industrial robots, according to the International Federation of Robotics (IFR).
One type of robot stands out for its dynamics: cobots, robots that work safely with humans. Whether they are articulated arms or mobile robots, cobots represent a small revolution in industrial robotics.
Unlike traditional industrial robots, which work away from humans, in a protective metal cage or suspended above the production line, cobots operate in the same workspace as humans. Supported by the cobots, humans are relieved of repetitive, boring and risky tasks, which improves their efficiency and well-being while reducing absenteeism.
Cobots also stand out for their versatility. They can be found both on assembly production lines and in the small workshops of SMEs. Increasingly, they are also found in warehouses, where they can be used to carry out a wide range of tasks. pick and place (moving goods from one place to another), palletising or packing. This is a response to the chronic labour shortage in these repetitive tasks of order preparation and packing.
What is a cobot?
The cobot takes its name from the contraction of " collaborative robot "or collaborative robot. This is a robot that works in collaboration with a human operator. Robot and human therefore share the same space.
The whole thing first cobot was designed in 1996 at the American university of Northwestern by professors James Colgate and Michael Peshkin. Their aim was to reduce the workload of employees at General Motors' car plants by automating strenuous tasks.
This first cobot was nothing extraordinary: a simple wheel and motor guided by a programme.
The first cobots came onto the market in the 2000s. Kuka Robotics, which also produces conventional industrial robots, launched its first cobot, the LBR 3, in 2004.
One of the leading manufacturers of cobots, the Danish company Universal Robotics, launched its first cobot, the UR5, in 2008.
The different types of cobots
What does a cobot look like? There are two main categories: articulated arms and mobile robots.
Robotic arms
Robotic arms are anthropomorphic robots in the form of arms capable of manipulating objects, assembling, screwing, welding, sanding, gluing, painting... or packaging. Thanks to their meticulous movements, they work with precision.
The UR16 robotic arm from Universal Robotics is capable of lifting 16 kilos.
So how do you choose? The main characteristics to consider are the maximum payload (from 2 to 30 kg depending on the model), the maximum working radius or reach (from 500 to 1500 mm approx.) and the number of axes, which will determine the robot's degree of freedom and flexibility, and the ability to reach more complex positions, making it suitable for a wider range of applications.
Mobile robots (AGV and AMR)
On their side, mobile robots are the big trend of the moment. We distinguish the Automated guided vehicles (AGVs) and autonomous mobile robots (AMR). The main difference between AMR and AGV is the navigation system. Whereas AGVs move along a predefined path using laser or wire guidance systems (buried wire), AMRs adapt their trajectory in real time in connection with the company's warehouse management software, which controls their movements.
Their role is mainly to move these goods. They can carry hundreds of kilos on each journey in complete safety for humans.
The differences between robots and cobots
Safety and human-friendliness
Operating in close proximity to humans means that the cobot has to be equipped with a whole range of safety systems in order to perceive its environment, know where humans are at all times, prevent any risk of collision and increase safety. Equipped with force and torque sensors (to adapt their power and speed), radar, lasers and cameras, cobots avoid any physical contact with humans. And if they do, they can automatically stop.
If it is alone, the cobot will advance on its task at full speed, but it will slow down as soon as a person approaches and will stop automatically if it is touched or if it detects an obstacle. It will resume its activity as soon as the person moves away.
Other elements contribute to safety: a deliberately low execution speed, a low mass (a few kilos) compared with industrial robots, rounded edges that do not protrude, low operating noise, soft, soothing colours (white, blue), etc.
The use of collaborative robots is governed by safety standards and regulations, in particular ISO 10218, which defines safety principles (safety stop, manual guidance, speed control, etc.) and ISO 15066:2016, which defines technical specifications (force and pressure thresholds, etc.) that manufacturers must comply with.
An affordable price
Smaller and easier to install, cobots are also much cheaper than traditional industrial robots. They cost between €10,000 and €50,000, up to ten times less than their industrial equivalent. As a result, their return on investment is very rapid, averaging around 195 days.
Ease of programming
Unlike a traditional industrial robot, a cobot is operational in record time. They are very simple to programme, simply using an application to describe the tasks to be carried out. No coding is required. Another possibility is learning-based programming, which is increasingly based on artificial intelligence and autonomous agentsThe robot can be taught what to do by manipulating it using the application.
In general terms, cobots adapt easily to new situations. parametersThey are more versatile than conventional industrial robots, adapting more easily to changes in workstation or production. They are more versatile than conventional industrial robots, and adapt more easily to changes in workstation or production.
Performances
A cobot will be less powerful than an industrial robot in order to minimise the risk of accidents with humans. With a reduced working speed and lighter workloads, between 3 and 30 kg depending on the model, their production volumes are lower. They are better suited to the manufacture of small series or precision work.
A new human-machine relationship
While industrial robots aim to improve the speed and quantity of production, cobots generate direct productivity gains, such as improving the performance of human operators who can concentrate on higher added-value tasks, as well as indirect gains such as improving the quality of processes and the safety and quality of life of workers.
Designed to lift and handle heavy loads, industrial robots work wonders on assembly tasks. Cobots, on the other hand, are particularly well suited to handling light loads, in finishing applications, assembling small parts (electronics), gluing and welding, moving parts (pick and place), quality control (chips, touch screen, etc.), handling, packaging and palletising.
So it's only natural that they should be found in the consumer goods and electronics industries, and working in warehouses to pack cartons.
Before implementing a cobotics solution, you need to think about its integration, as you would with any new technology. This involves analysing demand and requirements (workflows, production rates, etc.), analysing the work from the point of view of both workstations and ergonomics, and supporting teams to familiarise them with the robot so that the human-machine relationship runs as smoothly as possible.