A maintenance department repairs when a breakdown occurs. Yes, but managing problems on a case-by-case basis generates additional costs, production delays and, consequently, lower productivity, not to mention technician fatigue. Industrial maintenance therefore has a role to play in the economic stability of the industry of the future.
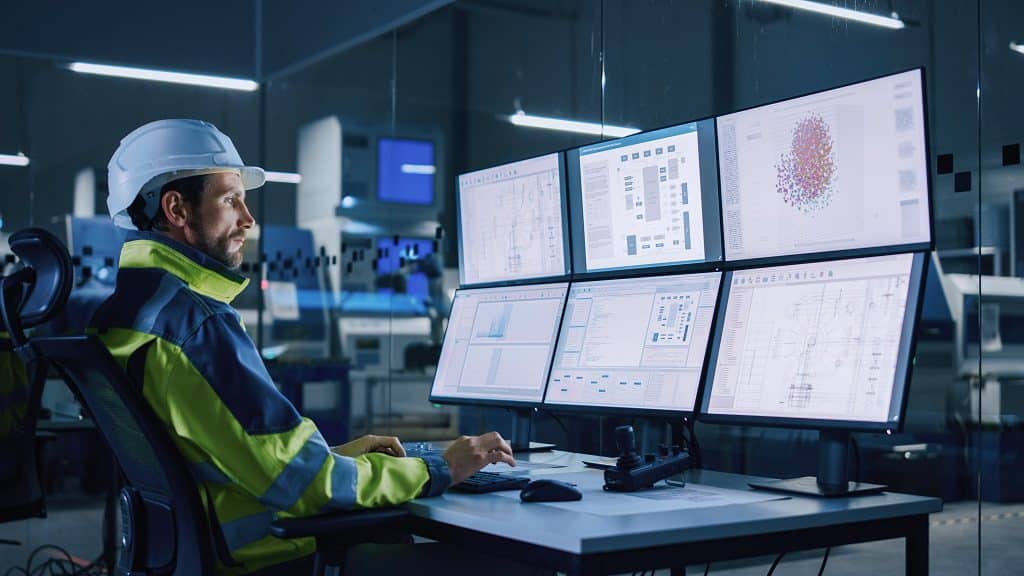
Industry is a constantly evolving sector. And to ensure stability and performance that are synonymous with longevity, it is vital for the industry to ensure that its wheels are well oiled. It is therefore essential for the industry to seek to improve its quality of service now and in the future. As a result, maintenance plays a key role in this performance-enhancing process. But how can a maintenance department be managed intelligently and effectively? Guy Besson, an expert in the organisation and reliability of industrial maintenance, explains how to move from corrective maintenance to preventive maintenance.
Preventive maintenance: what's at stake?
In the interests of economy and profitability, companies are looking to cut budgets. However, budget cuts (when they are well thought out) are not necessarily penalising. And it is this balance that characterises the challenges faced by maintenance departments, whose budgets tend to explode when breakdowns are managed on a case-by-case basis, without any real in-depth policy. So, a budget cut accompanied by a relevant improvement approach can bear fruit.
Launching a cost optimisation process meets the QCD objective: impeccable quality, optimised costs, deadlines met... by anticipating technical incidents rather than suffering from them. It is estimated that maintenance costs can represent up to 50 % production costs. A preventive approach would reduce costs and the number of breakdowns, with less investment in new machines and more effective mobilisation of technicians.
Structuring your preventive maintenance approach
Computers, mechanics... all devices, tools and machines require maintenance. This is a field that combines theoretical knowledge of the different types of machines, skills and technical and pragmatic know-how, often acquired through experience. But this knowledge gained through experience generally has one drawback: it is often more difficult to structure in a methodical and transferable way. But any maintenance approach requires a methodical approach.
The eight essentials of maintenance
These essentials ensure almost seamless organisation and are the first step towards an organised service:
- an equipment matrix produced and used ;
- resource efficiency (technicians, tools, suppliers);
- spare parts sorted and coded so you can find them in less than 1 minute;
- breakdown analyses carried out (using the right tools to understand the origin of breakdowns);
- setting up good monitoring indicators;
- lubricating and draining machines under supervision ;
- Drawing up procedures for all maintenance actions and processes carried out by the department (actions, nomenclatures, organisation, etc.);
- documentation that is organised and readily available.
Two pillars to structure these essentials
According to our expert, the dynamic generated by these eight essentials is accompanied by two pillars that cannot be neglected when it comes to optimising resources.
The first pillar is the matrix contained in the eight essentials. In fact, classifying machines (according to different criteria specific to the activity) makes it possible to obtain a list in order of criticality. So you know which machines are the most "at risk", or those that have priority in terms of in-depth maintenance work.
The second pillar is the 80/20 rule. In other words, 80% of the risks are concentrated on 20% of the machines most at risk. This rule allows for a more sustained maintenance and restoration policy, limiting the risk of breakdown and optimising the use of all these resources (tools, personnel, etc.).
The key is to be aware of these factors so as to reduce the workload and avoid being overwhelmed by avoidable breakdowns.
Mastering the five causes of breakdown
Whether for reasons of organisation, accountability or skills, repairs are no longer sufficient in an environment that demands competitiveness. Repeated breakdowns on the same machine considerably reduce the potential for profitability. Understanding the cause of a breakdown is therefore fundamental. In the field of maintenance, it's even the basis of a thorough job well done. In fact, knowing the cause of a breakdown enables you to find a solution and therefore control some of the risks.
- incorrect use of equipment: too fast, too loud, with the wrong material, etc.
- poor maintenance of the machine: this is the responsibility of the user, who must take care to clean it, notice wear and tear, etc.
- inadequate maintenance: a part not changed on time, a late oil change, etc.
- the human factor: often equated with a problem of skills, it can be a question of a poorly carried out repair, absent-mindedness, etc.
- a design fault.
"There's a solution for every problem", and that's exactly what this analysis does. A good understanding of a breakdown is the key to adequate maintenance resources.
Understanding problem solving
There are three key stages in problem solving:
- pose the problem;
- look for the key causes ;
- launch the action plan.
Once the diagnosis has been made, an effective and appropriate solution needs to be found. In other words, one that corresponds to the necessary investment that can be made (time, budget, resources, etc.) within the limits of what is cost-effective and enables the maintenance department to be effective. Three tools can meet this need:
- JDI: "just do it" is relevant for small problems that can be solved within the hour, without hierarchical validation, without ordering tooling, etc. A problem solved in one hour by a technician is an example. A problem solved in 1 hour by a technician.
- The MARP or Quick Kaizen method: the improvement wheel, derived from lean management, combines various problem-solving analysis and planning tools (QQOQCCP, the 5 whys, the Ishikawa diagram). It can be the start of an action plan and is therefore more suited to deep-rooted or repetitive maintenance problems. This method applies to problems of average complexity: 1 to 2 days for one or two technicians.
- 8D (D for discipline, i.e. "action to be taken"): this is an 8-step analysis method that structures decision-making in a continuous improvement process. Its different stages take into account all the facets of the problem to be solved, and above all call for a collaborative spirit. More structured, it is more suited to more complex problems involving different resources (quality department, design office, etc.), with three to five people and a longer planning horizon (around 1 to 4 months).
Organising the handling of breakdowns paves the way for "zero breakdowns" by structuring the approach and requiring a complete analysis of a problem in order to provide a lasting response.
Focus on training
Due to a lack of time and perspective, maintenance departments generally work on a just-in-time, corrective maintenance basis. However, to make real savings and achieve an attractive return on investment, companies need to switch to a preventive maintenance approach.
Training Deploying the TPM pillar: planned maintenance addresses the various tools for preventive maintenance, always drawing on the participants' professional experience. By drawing up personalised diagnoses and using collective intelligence, we aim to help participants carry out a methodical analysis of their breakdowns and draw up an action plan that is relevant to their business and their machines and meets their needs. And that's what our programme is all about: knowing how to adapt these different tools to troubleshooting while learning how to plan THE action plan that will save the company money.
Preventive maintenance has everything it takes to help industry improve performance and profitability. Thanks to appropriate methods and tools, investments will quickly have an effect on the work force of teams (and their motivation), as well as on the lifespan of machines. Last but not least, this maintenance policy is set to evolve as the industry evolves, with technological advances in particular making it possible in some cases to implement a policy of predictive maintenance.