Flexibles, légers, faciles à programmer et surtout moins chers que les robots classiques, les cobots gagnent en popularité, notamment dans les PME. Ces robots assistent les humains dans des tâches répétitives ou dangereuses : transport de charges, tri, emballage, assemblage, mesures et analyses… Rencontre avec ces travailleurs polyvalents et infatigables.
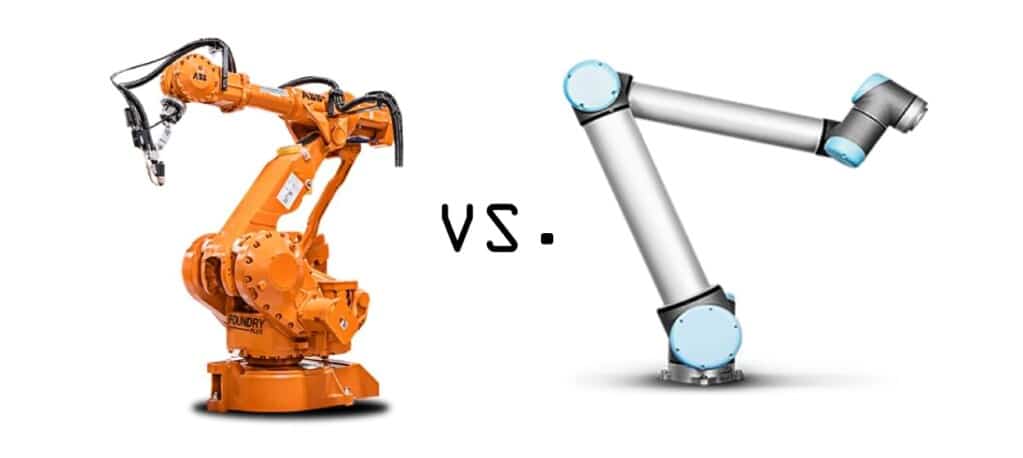
Les robots ne connaissent pas la crise. Jamais la France n’aura autant compté de robots dans ses usines. L’année 2022 a enregistré un record, avec une croissance de 13 % de robots industriels, selon la fédération internationale de robotique (IFR).
Un type de robot se distingue par sa dynamique : les cobots, ces robots qui travaillent en toute sécurité avec les humains. Que ce soient des bras articulés ou des robots mobiles, les cobots constituent une petite révolution dans la robotique industrielle.
Car, contrairement aux classiques robots industriels qui travaillent loin des humains, dans une cage métallique de protection ou suspendus au-dessus de la ligne de production, les cobots opèrent dans le même espace de travail que les humains. Épaulés par les cobots, les humains se retrouvent ainsi déchargés des tâches répétitives, ennuyeuse et à risque, ce qui améliore leur efficacité et leur bien-être tout en réduisant leur absentéisme.
Les cobots brillent également par leur polyvalence. On les retrouve aussi bien sur des chaînes de production de montage que dans de petits ateliers de PME. On les croise aussi de plus en plus dans les entrepôts pour faire du pick and place (déplacer la marchandise d’un endroit à un autre), de la palettisation ou de l’emballage. De quoi répondre à la pénurie chronique de main-d’œuvre sur ces tâches répétitives de préparation de commande et de colisage.
Qu’est-ce qu’un cobot ?
Le cobot tire son nom de la contraction de « collaborative robot » ou robot collaboratif. C’est un robot qui travaille en collaboration avec un opérateur humain. Robot et humain partagent donc le même espace.
Le tout premier cobot a été conçu en 1996 à l’université américaine de Northwestern par les professeurs James Colgate et Michael Peshkin. Leur objectif était de réduire la charge de travail des employés des usines d’automobile de General Motors en automatisant des tâches éprouvantes.
Ce premier cobot n’avait rien d’extraordinaire : une simple roue et un moteur guidés par un programme.
C’est dans les années 2000 que sont commercialisés les premiers cobots. La marque Kuka Robotics, qui produit également des robots industriels classiques, commercialise son premier cobot, le LBR 3 en 2004.
L’un des plus grands fabricants de cobots, le danois Universal Robotics, lance son premier cobot, l’UR5, en 2008.
Les différents types de cobots
À quoi ressemble un cobot ? Il existe deux grandes catégories : les bras articulés et les robots mobiles.
Les bras robotiques
Les bras robotiques sont des robots anthropomorphiques sous forme de bras capables de manipuler des objets, assembler, visser, souder, poncer, coller, peindre… ou emballer. Grâce à leurs gestes millimétrés, ils travaillent avec précision.
Le bras robotique UR16 d’Universal Robotics est capable de soulever 16 kilos.
Comment le choisir ? Les caractéristiques principales à prendre en compte sont la charge utile maximale (de 2 à 30 kg selon les modèles), le rayon de travail ou la portée maximale (de 500 à 1500 mm env.) et le nombre d’axes qui va déterminer le degré de liberté et la flexibilité du robot, la possibilité d’atteindre des positions plus complexes ce qui le rend apte à un plus large éventail d’applications.
Les robots mobiles (AGV et AMR)
De leur côté, les robots mobiles sont la grande tendance du moment. On distingue les véhicules à guidage automatique (AGV) et les robots mobiles autonomes (AMR). La principale différence entre AMR et AGV réside dans le système de navigation. Alors que les AGV se déplacent le long d’un chemin prédéfini à l’aide de systèmes de guidage laser ou filoguidé (fil enterré), les AMR adaptent leur trajectoire en temps réel en connexion avec le logiciel de gestion d’entrepôt de l’entreprise qui pilote leurs mouvements.
Leur rôle est principalement de déplacer ces marchandises. Ils peuvent convoyer des centaines de kilos à chaque voyage en toute sécurité pour les humains.
Les différences entre robots et cobots
La sécurité et le côté « human friendly »
Évoluer à proximité des humains nécessite que le cobot embarque toute une panoplie de systèmes de sécurité afin de percevoir son environnement, savoir à tout moment où sont les humains, prévenir tout risque de collision et accroître la sécurité. Bardés de capteurs de force et de couple (pour adapter leur puissance et leur vitesse), de radars, de lasers ou de caméras, les cobots évitent tout contact physique avec un humain. Et, si par malheur cela se produit, ils peuvent se mettre automatiquement à l’arrêt.
S’il est seul, le cobot avance sur sa tâche à plein régime, mais il ralentira dès qu’une personne s’approche et s’arrêtera automatiquement si on le touche ou s’il détecte un obstacle. Il reprendra son activité dès que la personne s’éloignera.
D’autres éléments contribuent à la sécurité : une vitesse d’exécution volontairement réduite, une masse peu élevée (quelques kilos) comparée à celle des robots industriels, des bords arrondis et non saillants, un bruit de fonctionnement peu élevé, des couleurs douces et apaisantes (blanc, bleu), etc.
Des normes et des règles de sécurité viennent encadrer l’usage des robots collaboratifs, notamment la norme ISO 10218 qui définit les principes de mise en sécurité (arrêt de sécurité, guidage manuel, contrôle de la vitesse…) et la norme ISO 15066 :2016 qui définit des spécifications techniques (seuils de force et de pression…) que les fabricants doivent respecter.
Un prix abordable
Plus petits et plus simples à installer, les cobots sont aussi beaucoup moins chers que les robots industriels traditionnels. Comptez entre 10 000 et 50 000 euros environ, soit jusqu’à dix fois moins que leur équivalent industriel. Du coup, leur retour sur investissement est très rapide, environ 195 jours en moyenne.
La facilité de programmation
À la différence d’un robot industriel traditionnel, un cobot est opérationnel en un temps record. Très simples à programmer, il suffit de passer par une application pour lui décrire les tâches à accomplir. Aucun code n’est nécessaire. Autre possibilité : la programmation par apprentissage, basée de plus en plus sur l’intelligence artificielle et des agents autonomes, permet d’apprendre au robot les gestes à faire en le manipulant à l’aide de l’application.
De manière générale, les cobots s’adaptent facilement à de nouveaux paramètres, à de nouveaux environnements de travail, à de nouvelles pièces à traiter. Ils sont plus polyvalents que les robots industriels classiques et s’adaptent plus facilement à des changements de poste ou de production.
Les performances
Un cobot sera moins performant qu’un robot industriel afin de minimiser les risques d’accident avec les humains. Avec une vitesse de travail réduite et des charges de travail plus légères, entre 3 et 30 kg selon les modèles, leurs volumes de production sont moindres. Ils sont plus adaptés à la fabrication de petites séries ou au travail de précision.
Une nouvelle relation homme-machine
Alors que les robots industriels visent à améliorer la vitesse et les quantités de production, les cobots engendrent des gains de productivités directs comme la performance des opérateurs humains qui se concentrent sur des tâches à plus forte valeur ajoutée, mais aussi des gains indirects comme l’amélioration de la qualité des processus ainsi que la sécurité et la qualité de vie des travailleurs.
Conçus pour soulever et manipuler des charges lourdes, les robots industriels font des merveilles sur des tâches d’assemblage. De leur côté, les cobots sont particulièrement adaptés aux ports de charges faibles, dans des applications de finition, d’assemblage de petites pièces (électronique), de collage-soudage, de déplacement de pièces (pick and place), de contrôle qualité (puces, écran tactile…), de manutention, d’emballage et de palettisation.
On les retrouvera donc tout naturellement dans l’industrie des biens de consommation, l’électronique et au travail en entrepôts pour la mise en carton.
Avant de mettre en place une solution de cobotique, il faudra réfléchir à son intégration, comme pour toute nouvelle technologie. Cela nécessite d’analyser la demande et le besoin (flux, cadences…), analyser le travail tant du point de vue du poste que de l’ergonomie, accompagner les équipes pour les familiariser avec le robot afin que la relation homme-machine se passe au mieux.