Souvent incompris voire méconnu, le lean est pourtant une méthode possédant de nombreux avantages pour l’organisation des entreprises. Entre besoin d’agilité et nécessité d’optimisation, le lean apparaît comme la solution conciliant le mieux ces deux objectifs d’amélioration. Pour ORSYS, Hugo Maisonnial fait le point sur le lean comme levier d’amélioration continue.
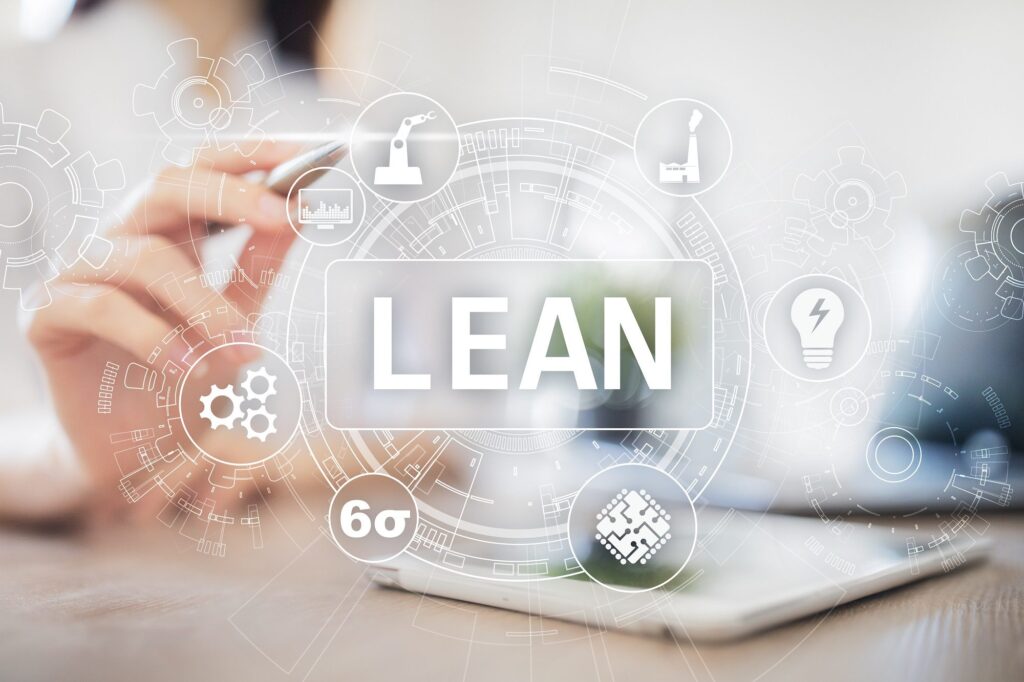
Être lean, c’est être « svelte »
Initié par Toyota dans les années 1950, le lean vise à l’identification et à l’élimination des gaspillages. Autrement dit, il s’agit de supprimer ou de transformer toutes les activités, tout le temps que nous passons à faire quelque chose, toutes les ressources (matérielles et humaines) que nous utilisons, et qui n’ont pas de valeur ajoutée pour le client, l’entreprise ou les employés.
Au terme « lean », trop souvent associé à des activités de « dégraissage » (en raison d’une traduction hasardeuse : mince/maigre), on préfère celui de « svelte », c’est-à-dire : faire « mieux » avec les mêmes ressources, tout en plaçant l’humain au cœur de la démarche.
Pensé sur le long terme, le lean possède de véritables atouts pour la globalité des activités de l’entreprise. Il instaure une démarche pérenne, favorise une organisation stable et collective, lutte contre le gaspillage. Il facilite aussi la digitalisation en poussant, par exemple, naturellement à la dématérialisation.
Le lean n’est pas réservé à l’industrie
Historiquement, le lean s’est d’abord largement déployé dans différentes industries (automobile, aéronautique, pharmaceutique…). Aujourd’hui, l’ensemble des secteurs d’activité est susceptible de s’appuyer sur cette méthodologie (services publics, entreprises de service, secteur bancaire…).
Dans tous les métiers et dans toutes nos activités, nous réalisons un enchaînement de tâches permettant d’amener le produit, le service ou l’information vers l’état souhaité par le client : on parle de « processus ». Chacune de ces étapes successives apporte de la valeur ajoutée mais peut aussi présenter des gaspillages. À ce stade émergent alors des pistes d’amélioration. Or, c’est bien cette notion d’optimisation que privilégie le lean.
En clair, le lean ne prend pas en compte un domaine d’activité mais un processus. Il est donc applicable partout, tout le temps, sous réserve d’en comprendre les enjeux et d’en maîtriser les outils.
Le lean en tant que culture d’amélioration continue
Le lean est avant tout une culture identifiée principalement par des comportements qui eux-mêmes découlent de l’utilisation d’outils. Il s’appuie sur quatre piliers : le travail en équipe, la communication, l’utilisation efficiente des ressources et l’élimination du gaspillage.
Pour une mise en application réussie, il est alors primordial :
– de définir la politique de déploiement d’amélioration continue au niveau de l’entreprise et de communiquer une vision claire (par exemple : améliorer la qualité/réduire les délais) ;
– d’aligner l’ensemble de l’organisation sur un objectif commun ou, autrement dit, d’impliquer le plus grand nombre ; – de développer un état d’esprit d’amélioration continue. En pratique, il s’agit de remettre en cause les processus et non les personnes.
Accompagner le changement pour pérenniser la démarche lean
Le lancement d’une démarche lean dans l’entreprise peut rencontrer des freins, en particulier lors de projets de transformation. Assez « classiquement », on retrouve les difficultés rencontrées en gestion du changement :
– pas de vision d’entreprise = nous sommes dans la confusion ;
– pas de savoir-faire = nous sommes dans l’anxiété ;
– sans motivation = nous sommes dans un changement lent ;
– pas de ressources = nous sommes dans la frustration ;
– pas de plans d’actions = faux départs.
La vigilance s’impose donc à toutes les étapes du projet et, en particulier, après les phases de déploiement. Pour pérenniser la démarche lean, il faudra s’assurer que l’amélioration continue est pleinement ancrée dans la culture de l’entreprise.
Les outils, c’est bien. La culture, c’est mieux.
La “boîte à outils” du lean est riche et variée. On y trouve notamment des outils :
– dits « fondamentaux » (5S, Management Visuel, standardisation…) ;
– de cartographie de processus (SIPOC, diagramme Swimlane, VSM…) ;
– visant à la résolution de problèmes (Ishikawa, 5 Pourquoi, QRQC…) ;
– de « Juste-à-Temps » (Kanban, Takt Time, Flux poussé/tiré…) ;
– stratégiques, comme « Hoshin Kanri » pour déployer la vision d’entreprise.
On entend souvent que le lean repose sur le « sens pratique ». C’est vrai, mais… En fonction de nos expériences (jeune diplômé ou personne très expérimentée) ou de notre culture (américaine, coréenne, française…), nous n’avons peut-être pas tous le même « sens pratique ».
Au-delà des outils, le lean est avant tout un état d’esprit.Celui de percevoir les problèmes comme des opportunités de s’améliorer.